Automation1 MDK Motion Development Kit
Built for power and ease of use, the Automation1 Motion Development Kit (MDK) is the most user-friendly interface available for industry-leading precision motion control. Drastically reduce your system setup and deployment time – in some cases from days to minutes.
Tools like the Machine Setup wizard, MachineApps HMI builder, the modern AeroScriptâ„¢ programming language and a digital oscilloscope enable you to set up, program and optimize servo and stepper motors, precision stages, galvo scanning systems and more in one development environment.
The Automation1 MDK includes the Studio application, Status Utility application, Console application, .NET API, C API, Python API and help files.
Have questions? Contact an Aerotech expert.
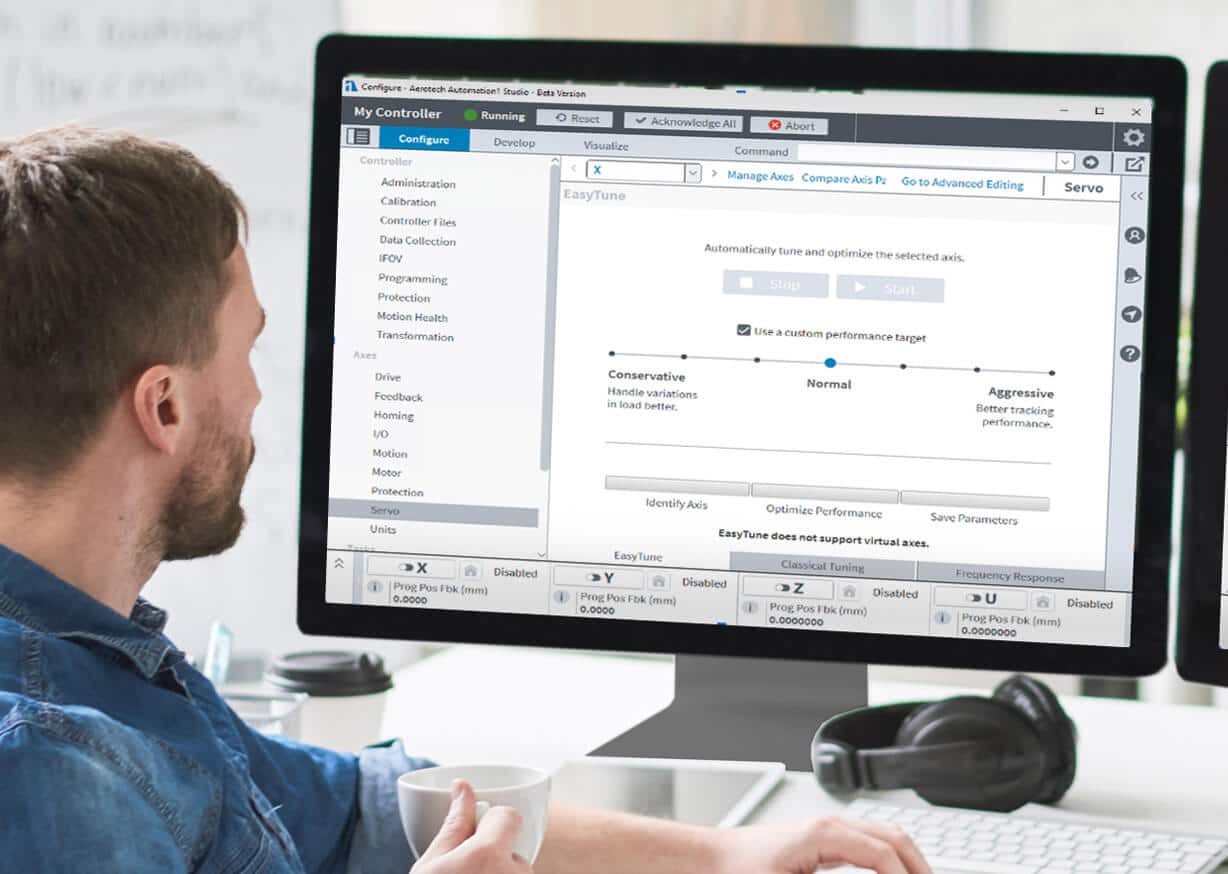
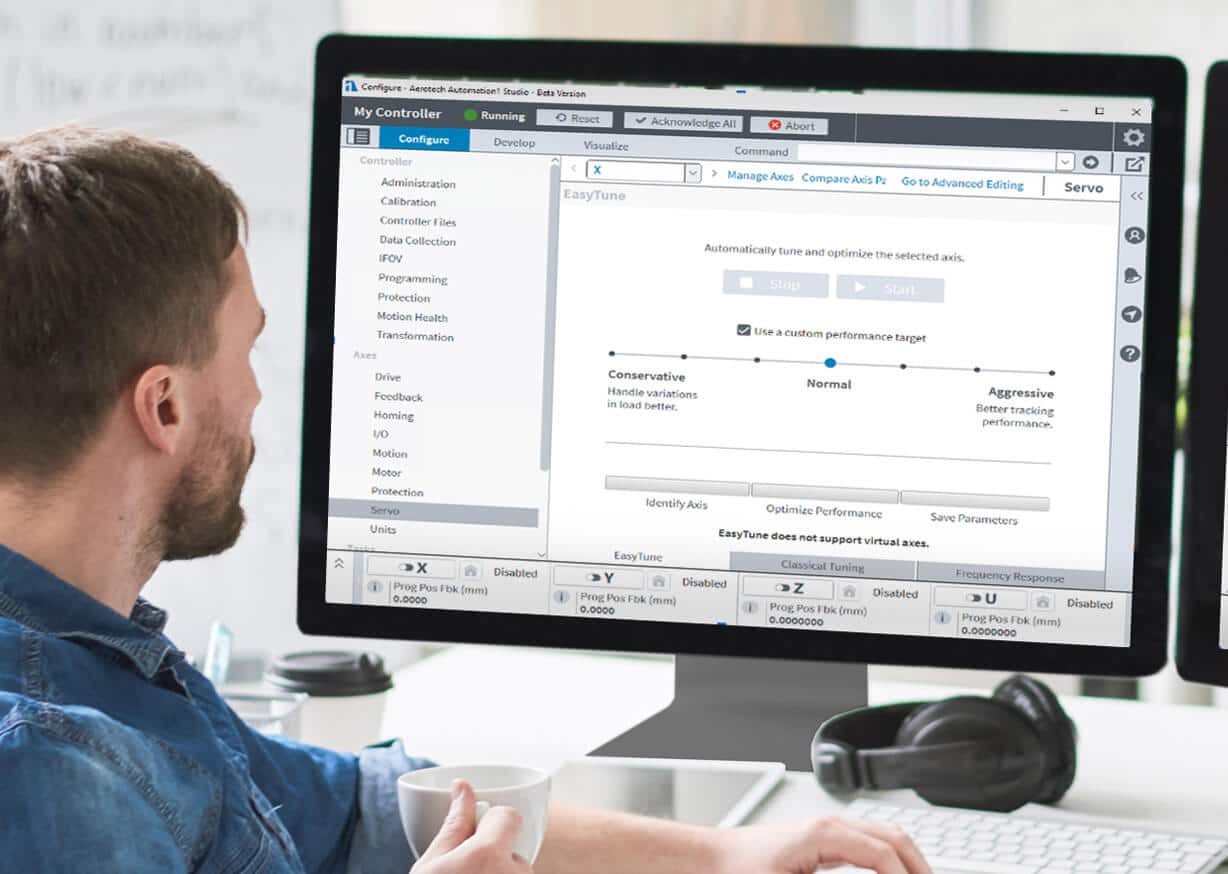
Key Features
Quickly add drive electronics and precision motion control mechanics to your motion control system via the Machine Setup wizard. When connected via the HyperWire™ bus, motor drives are automatically identified and added making motion control accessible to professional development teams as well as students and academics.
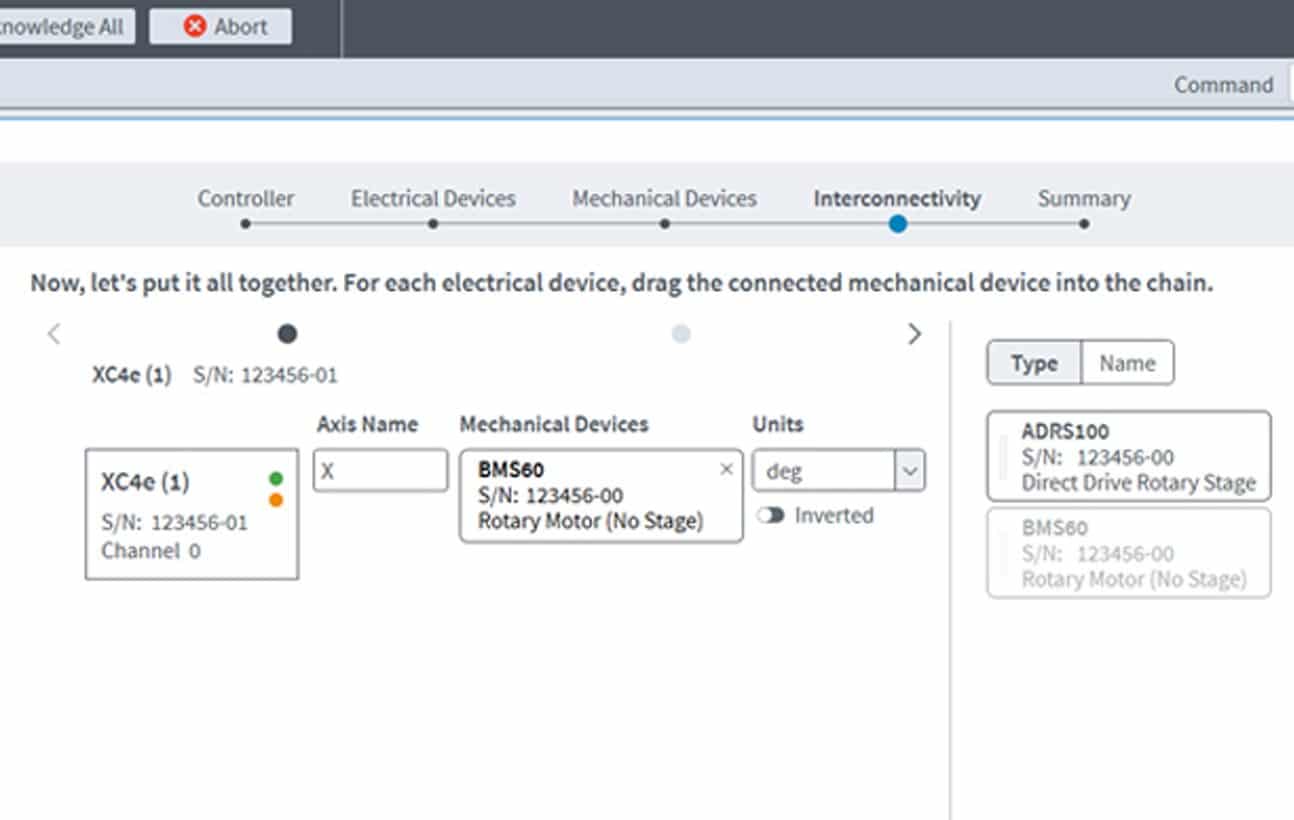
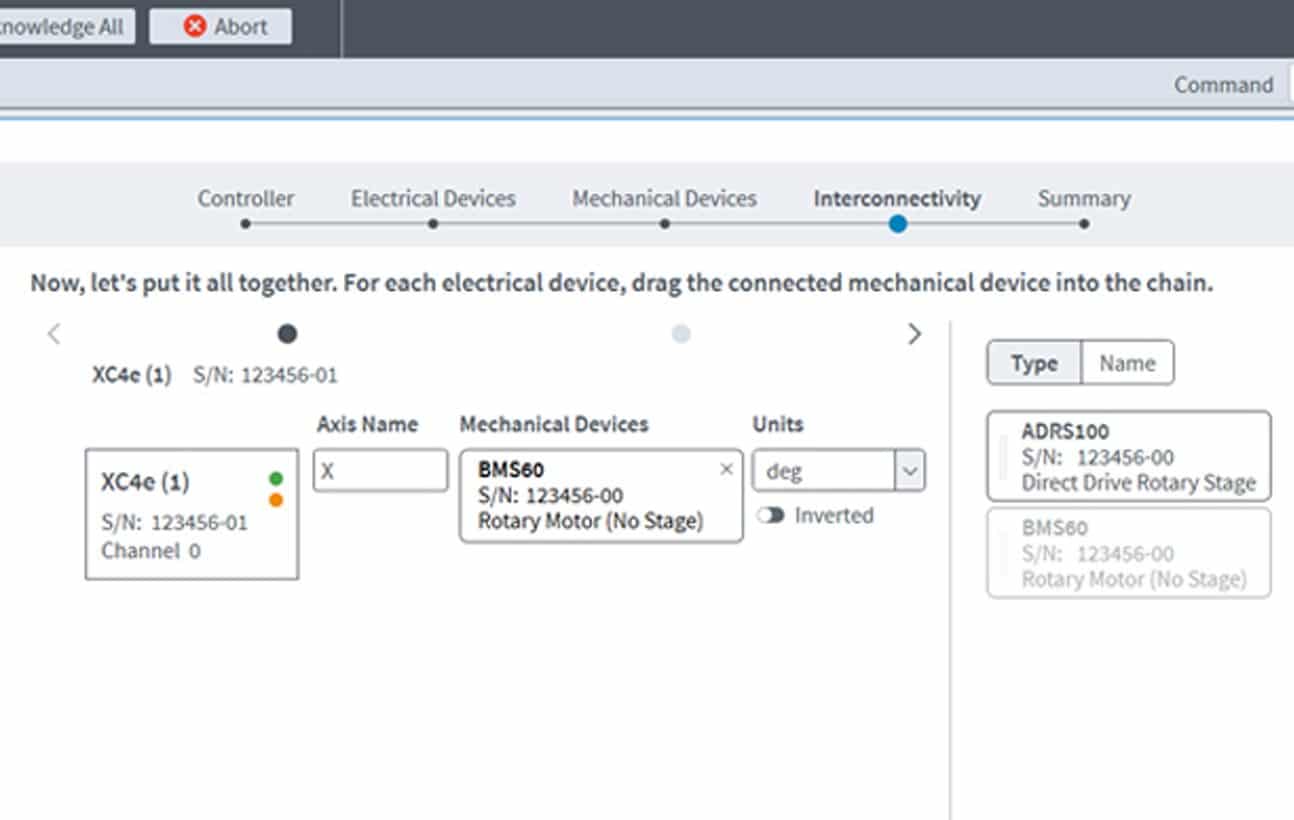
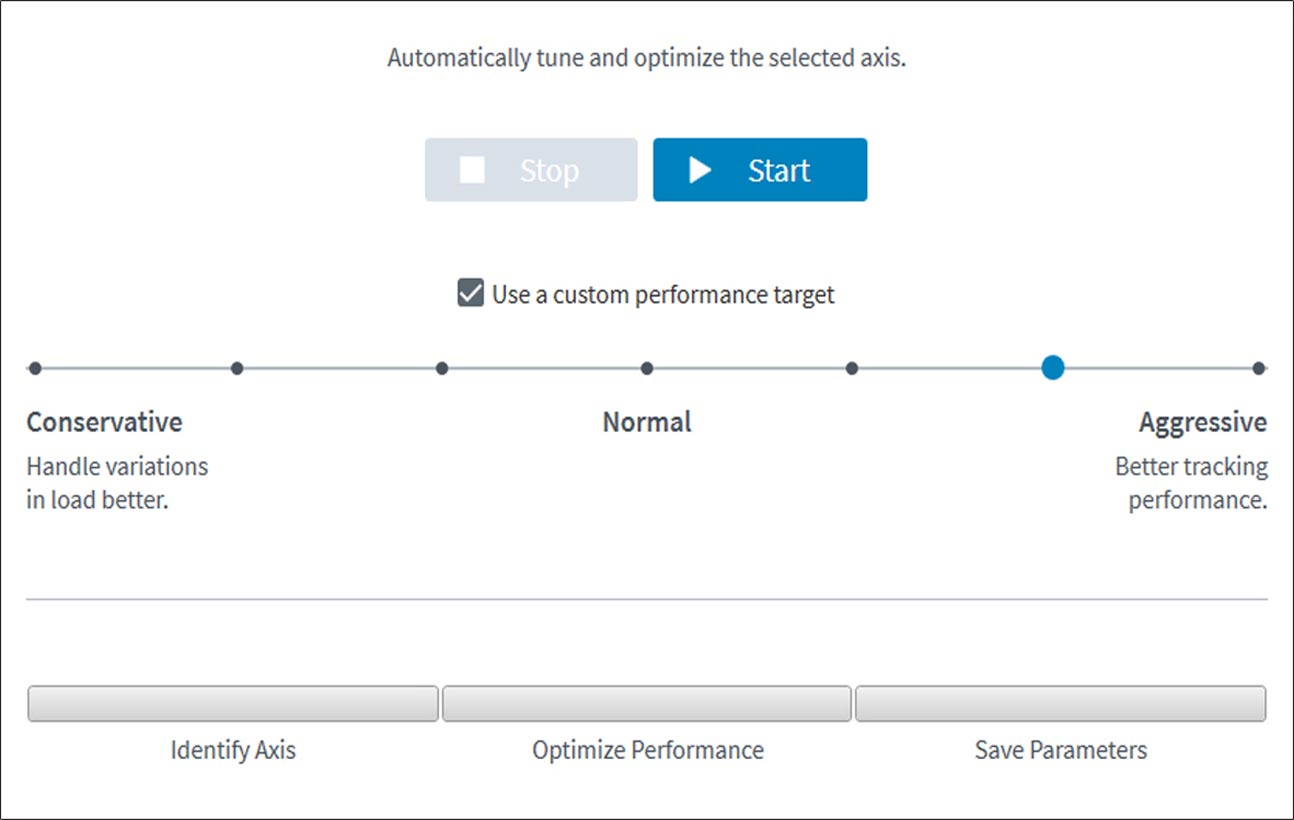
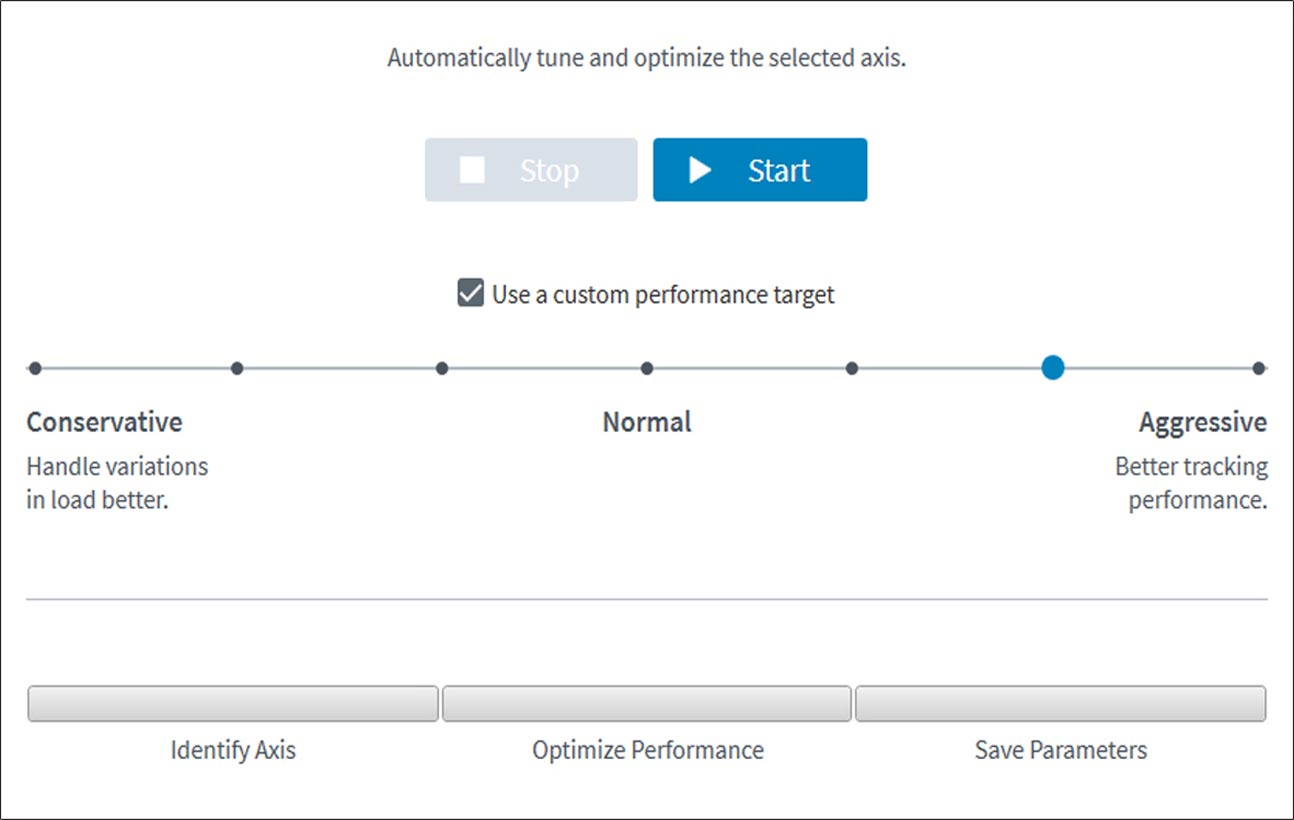
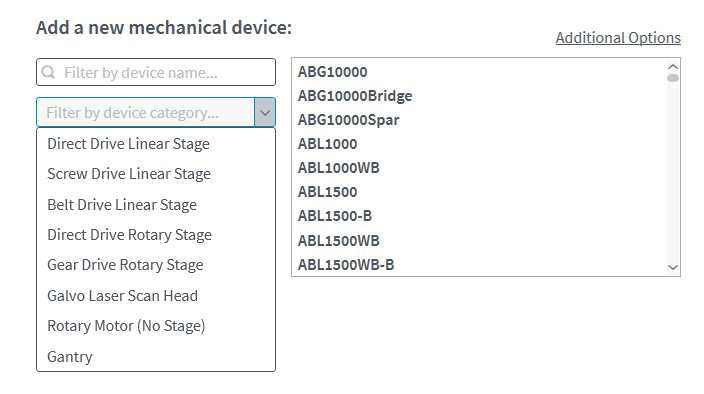
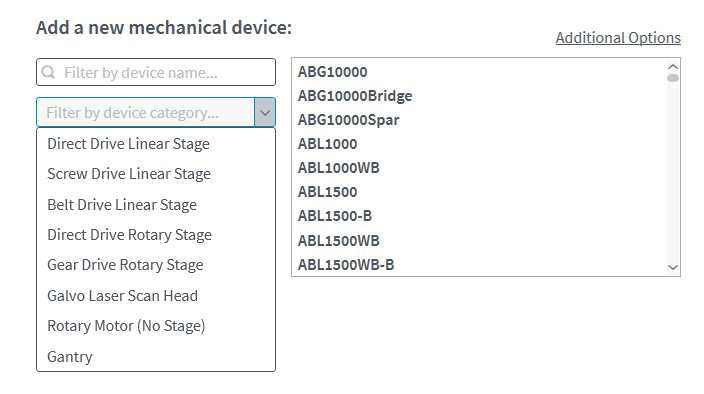
Our AeroScriptâ„¢ programming language integrates motion, G-code and process control commands into a single language for precision automation. AeroScript features arrays, structures, libraries and several other modern features.Â
Use AeroScript to program meaningful process control as well as realistic motion for the Automation1 software-based motion controller.   Â
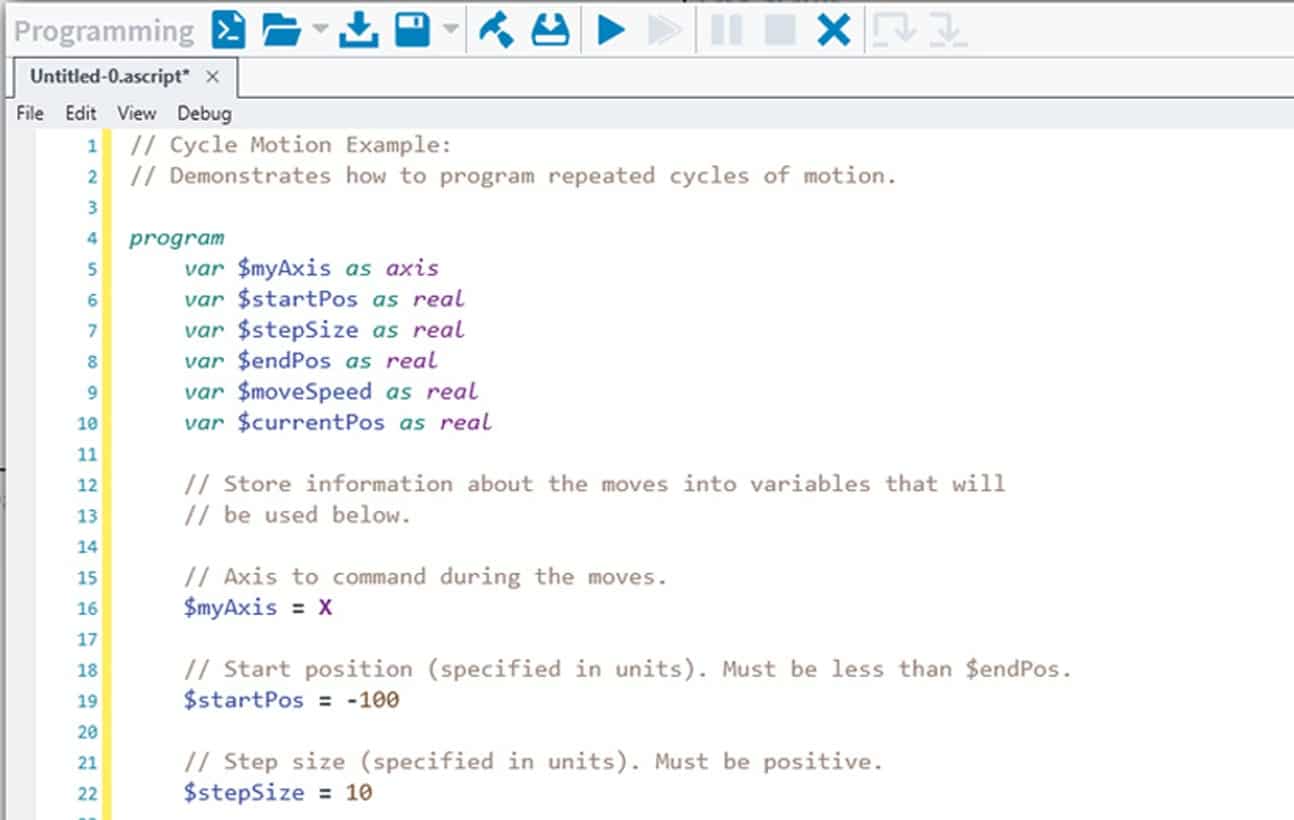
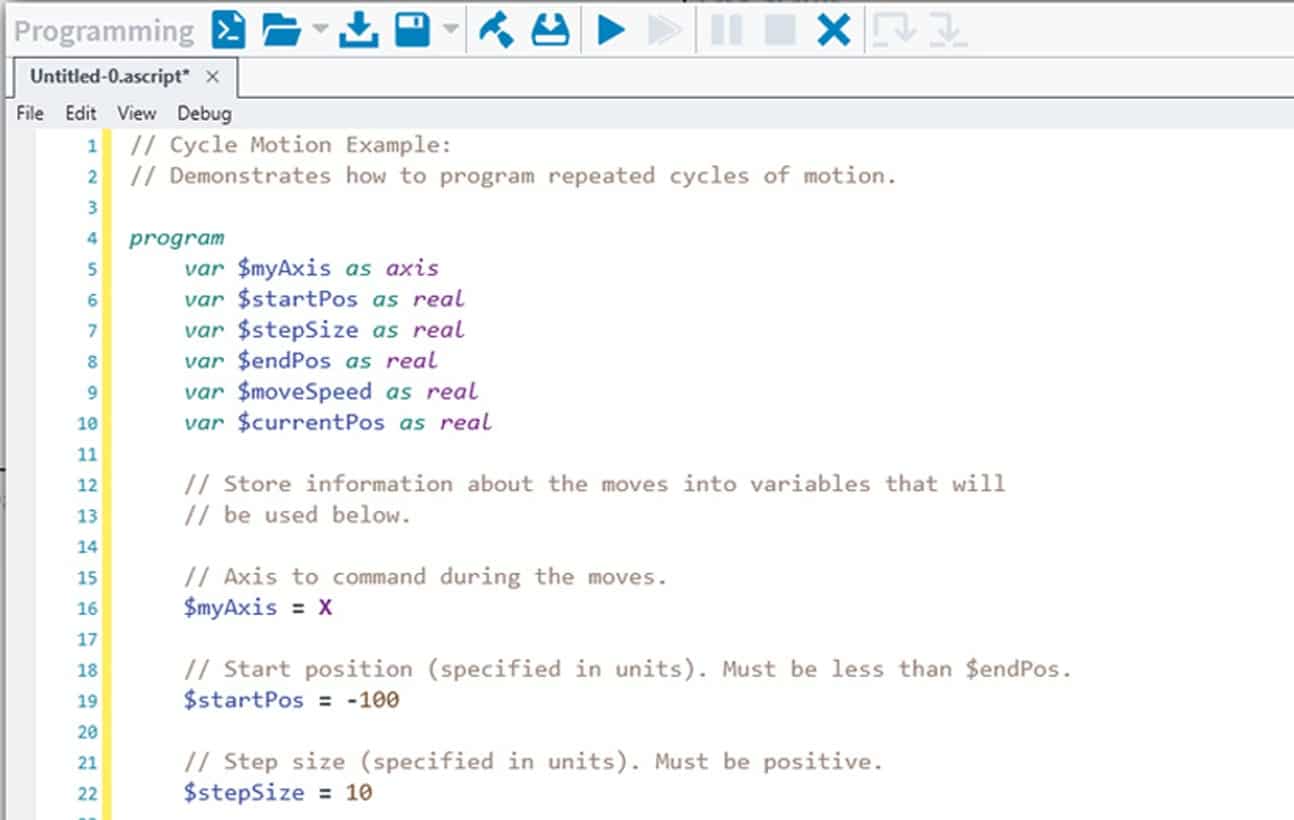
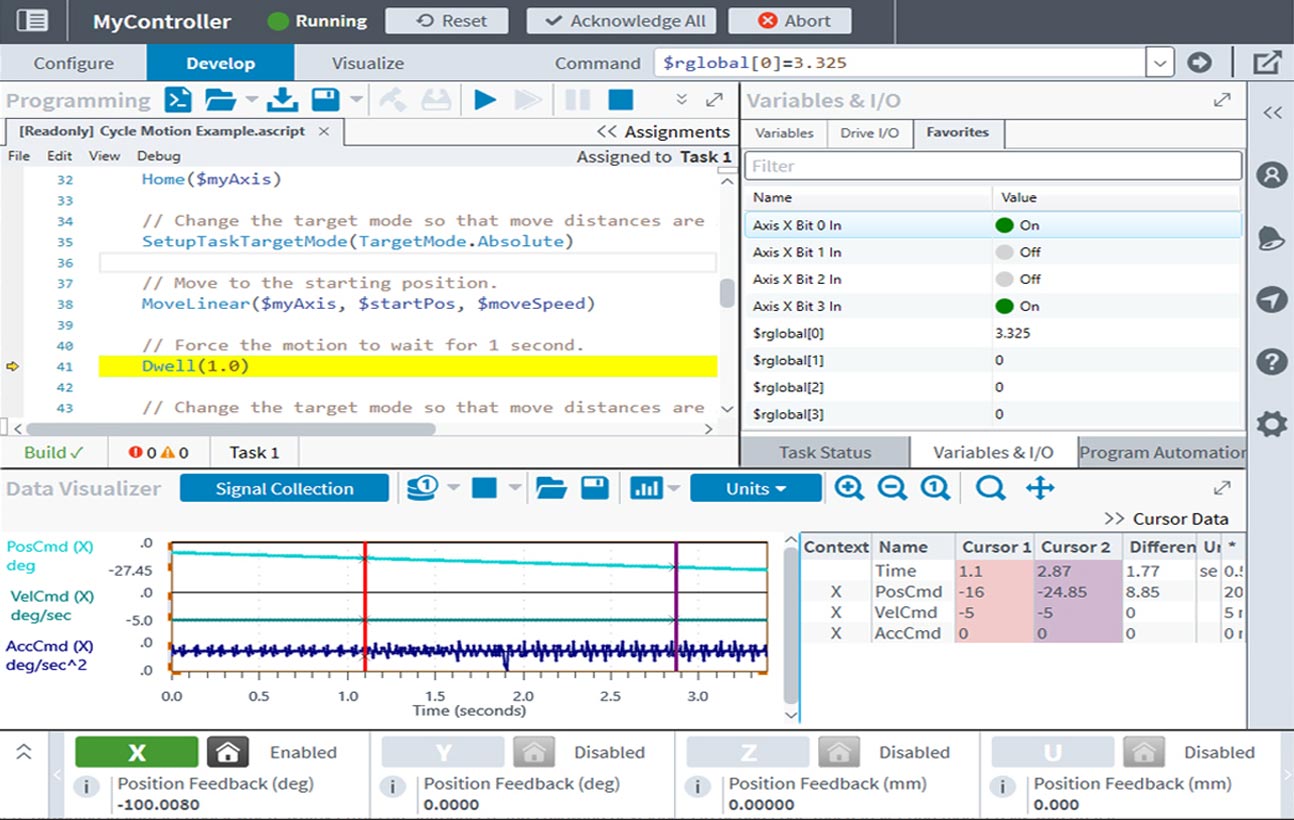
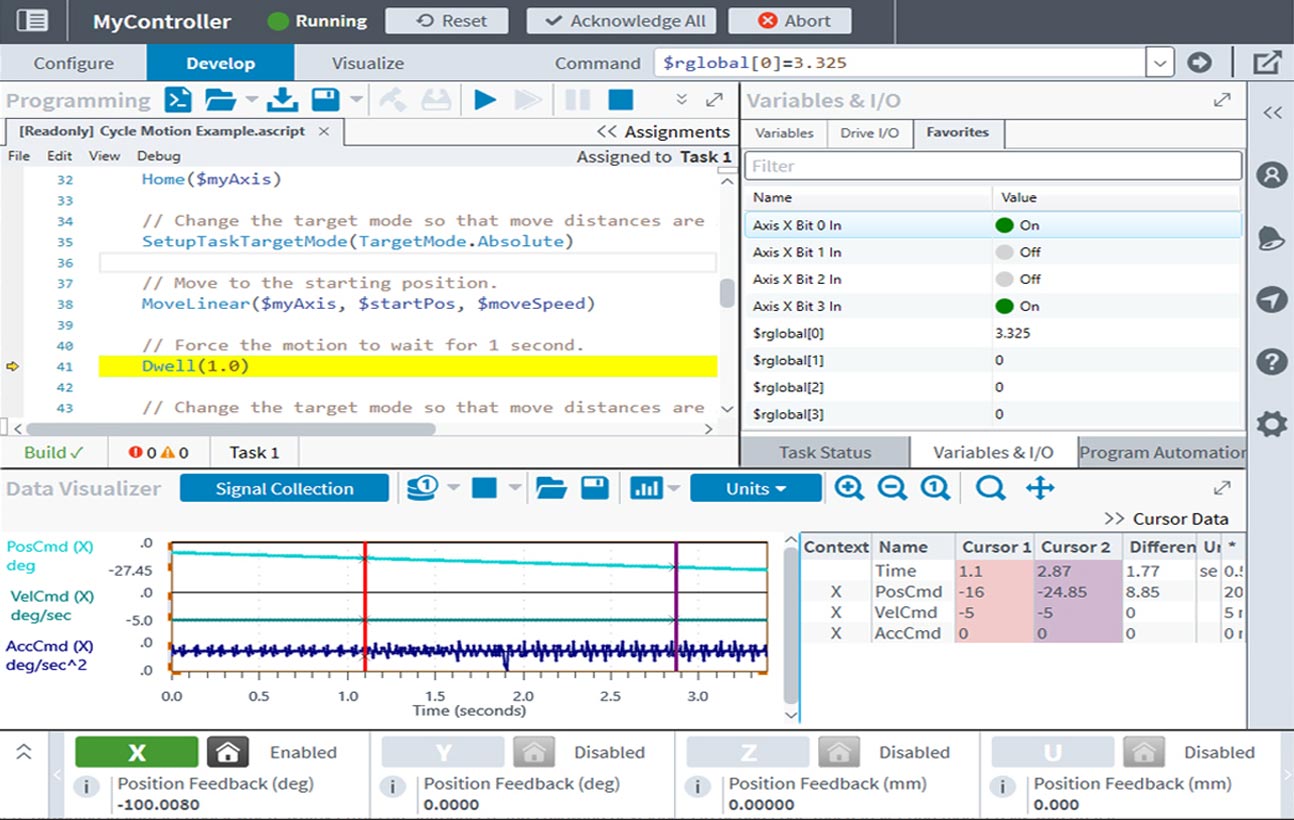
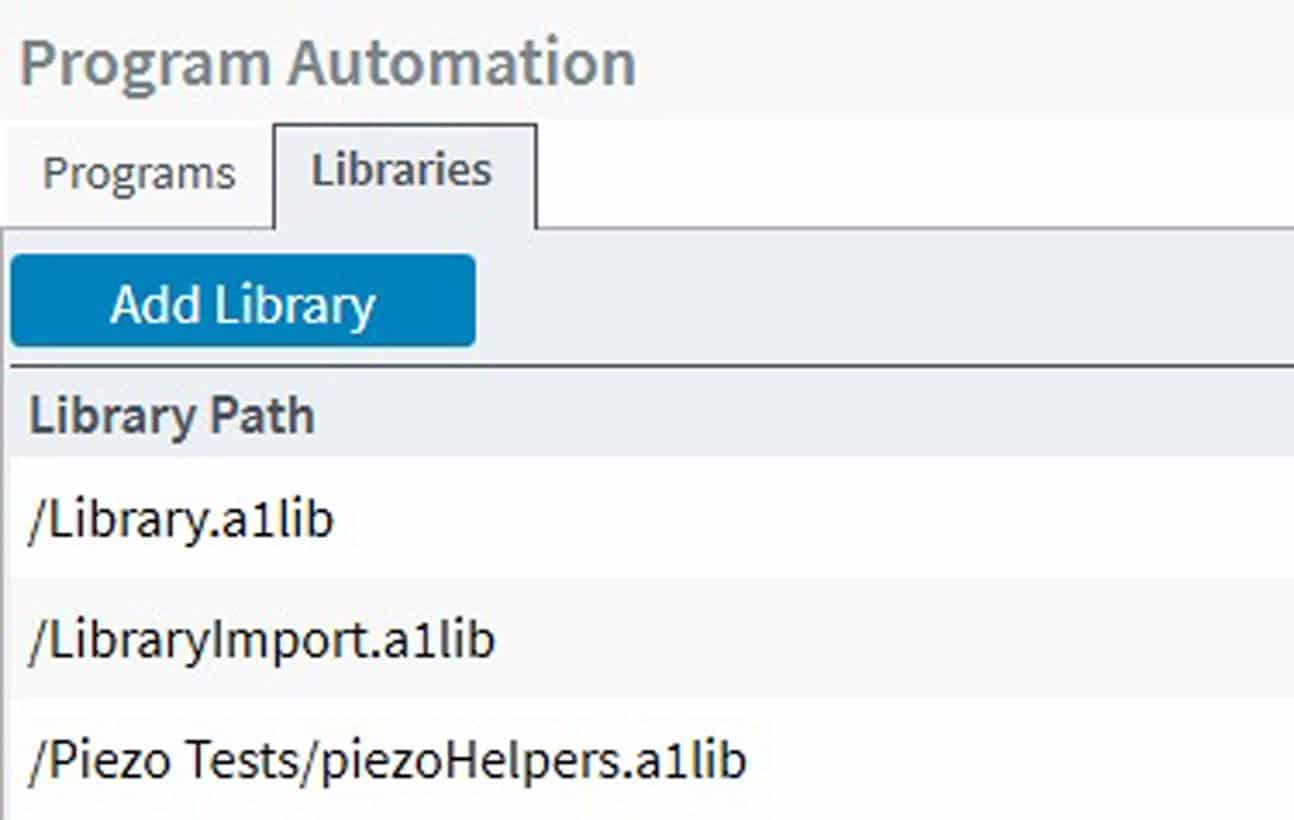
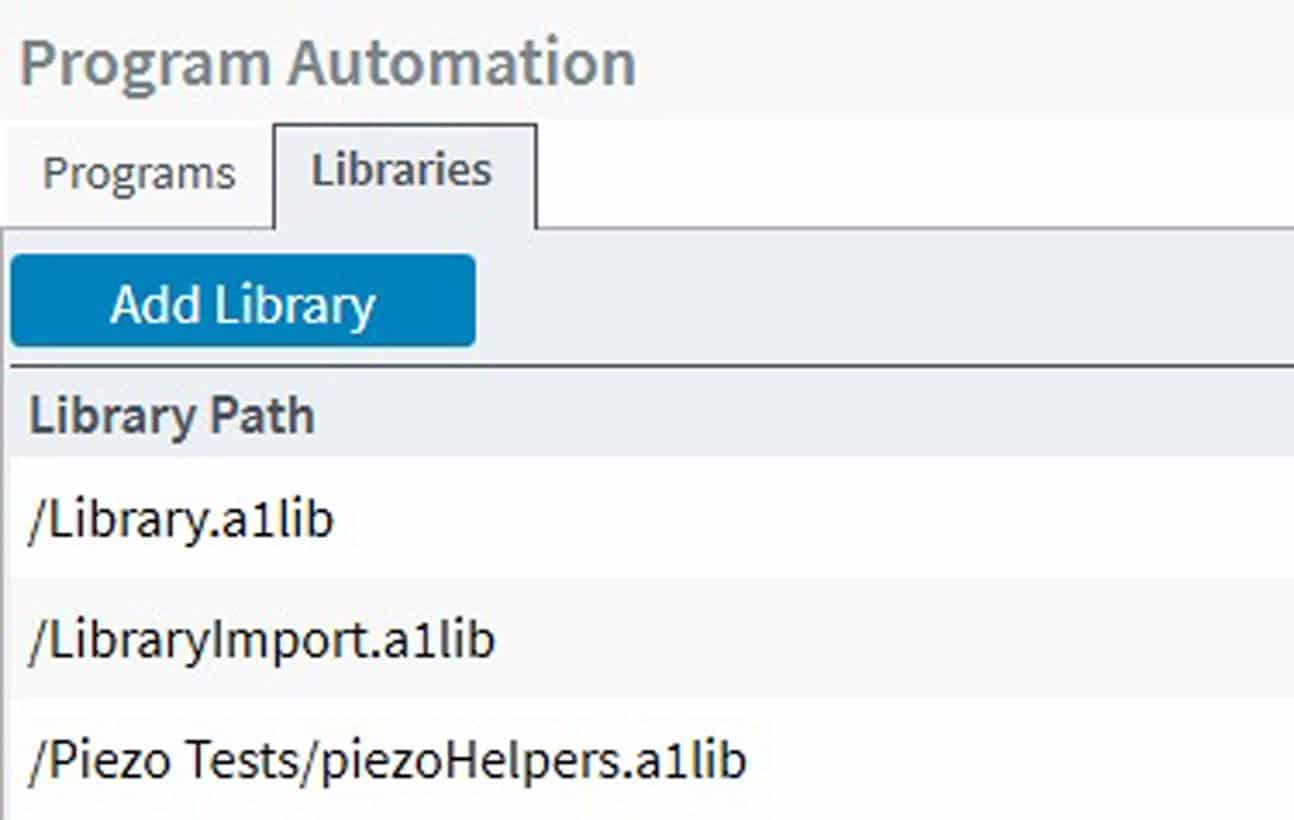
Analyze machine performance data with the Data Visualizer, a powerful digital oscilloscope with access to hundreds of signals from your controller and drives. View data in 1D, 2D and in the frequency domain. View feedback from actual motor drives or perform a motion simulation with virtual axes of motion control.Â
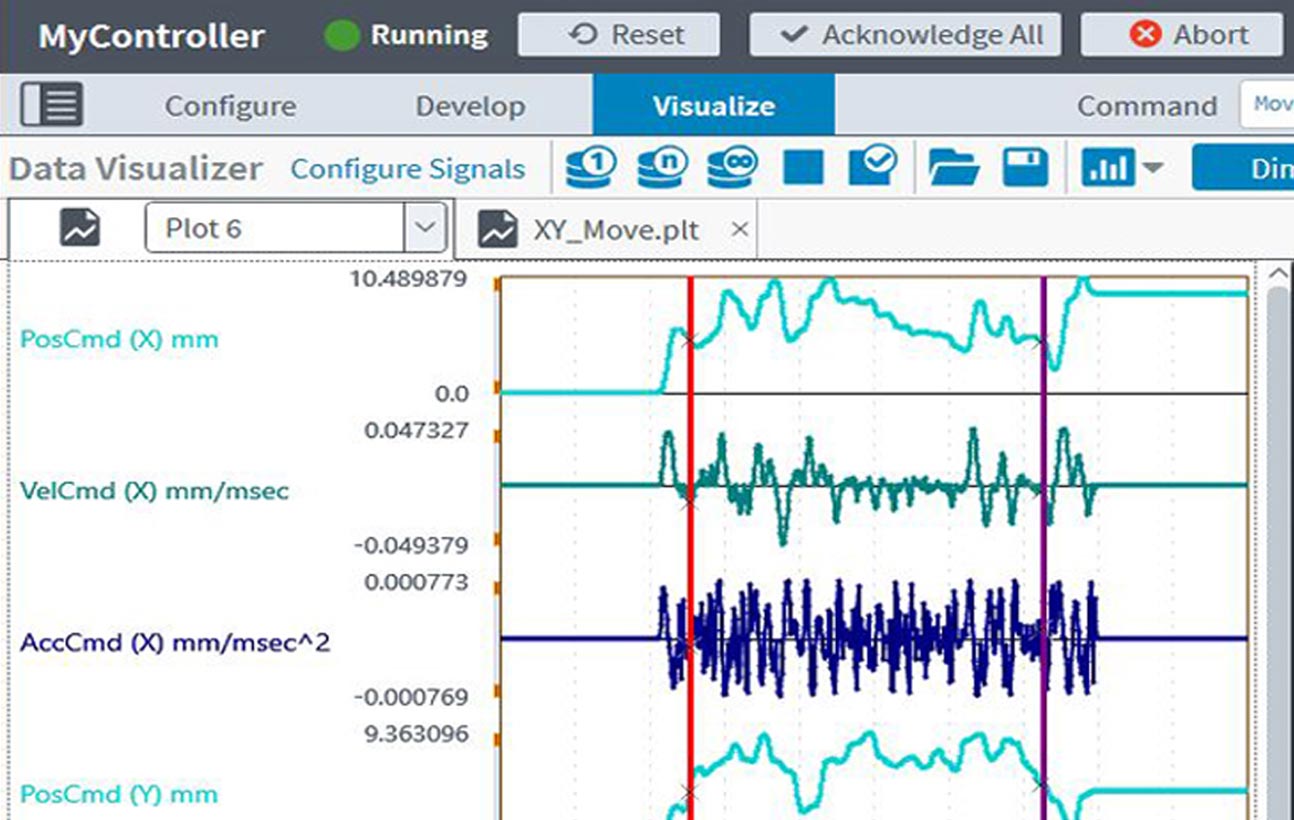
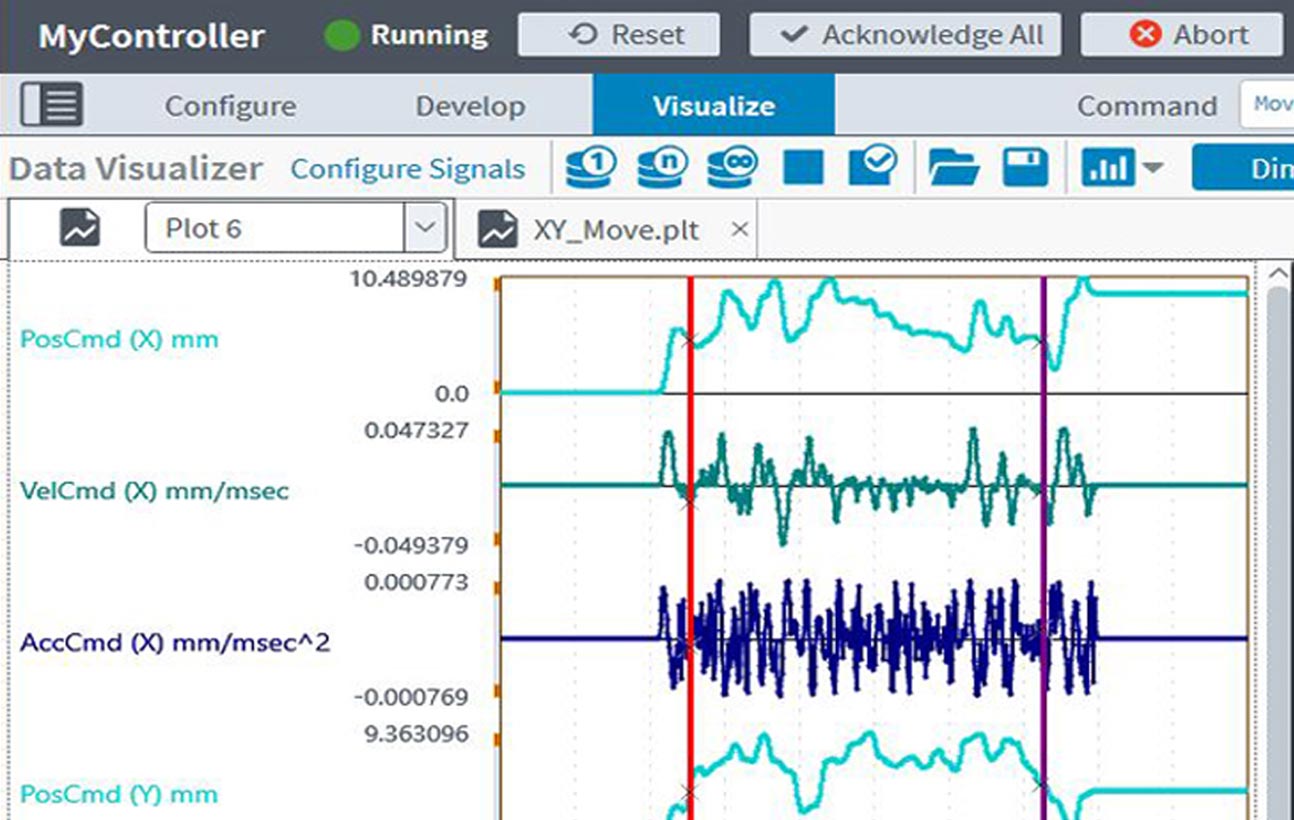
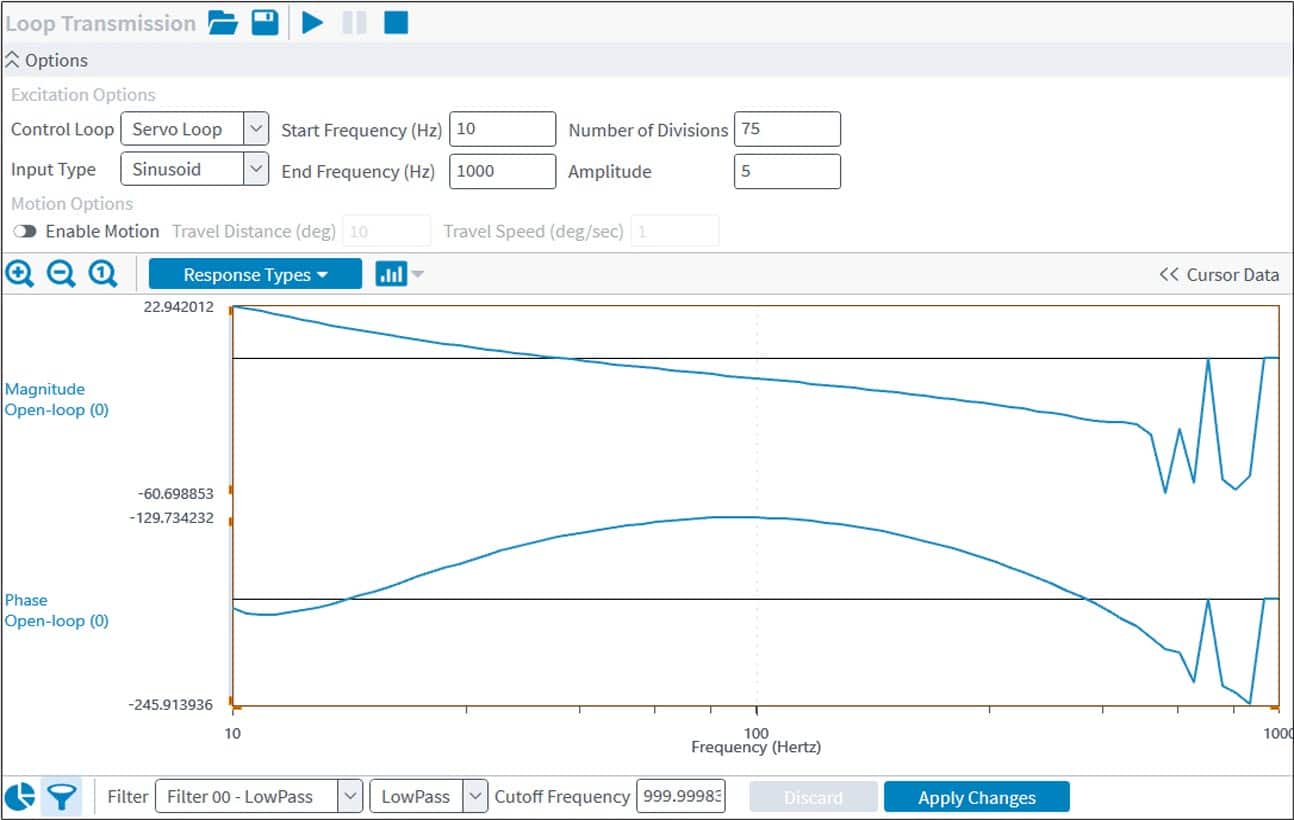
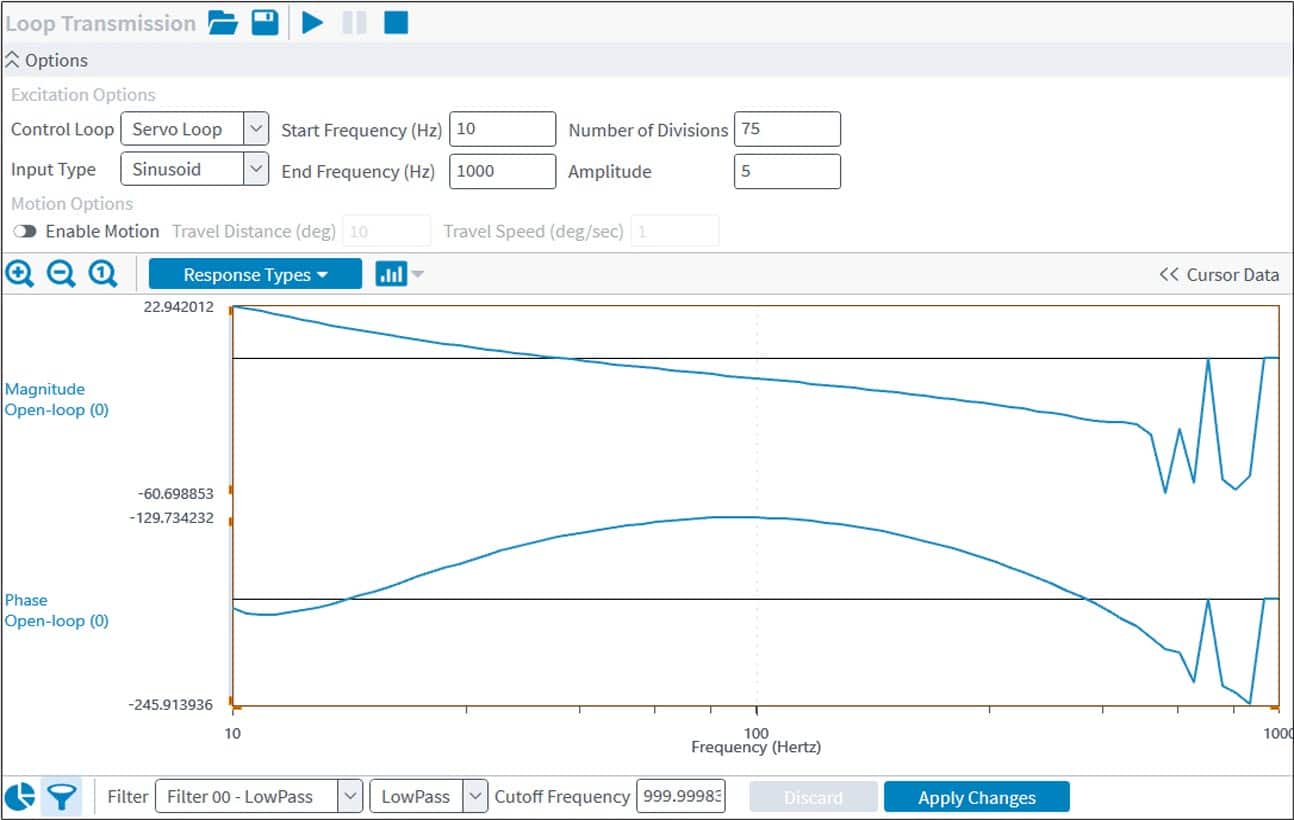
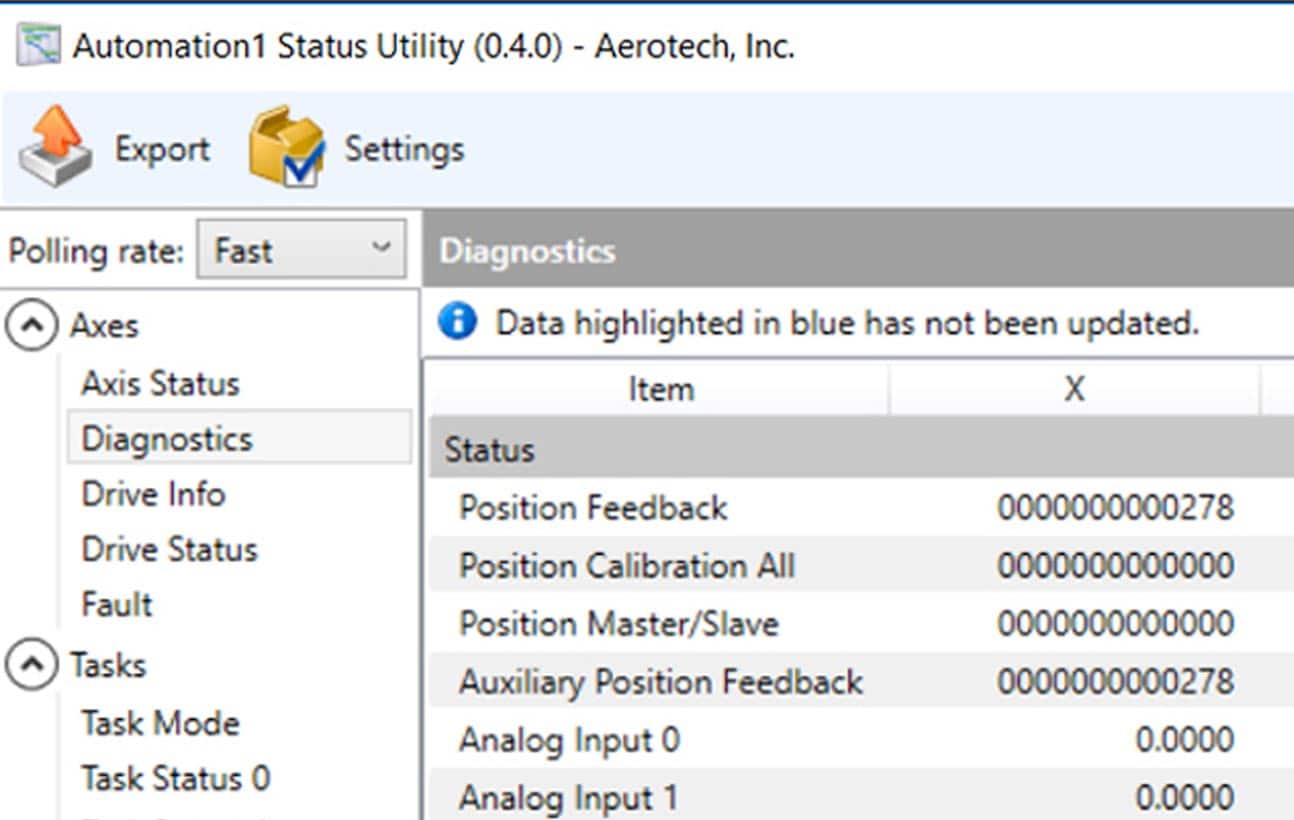
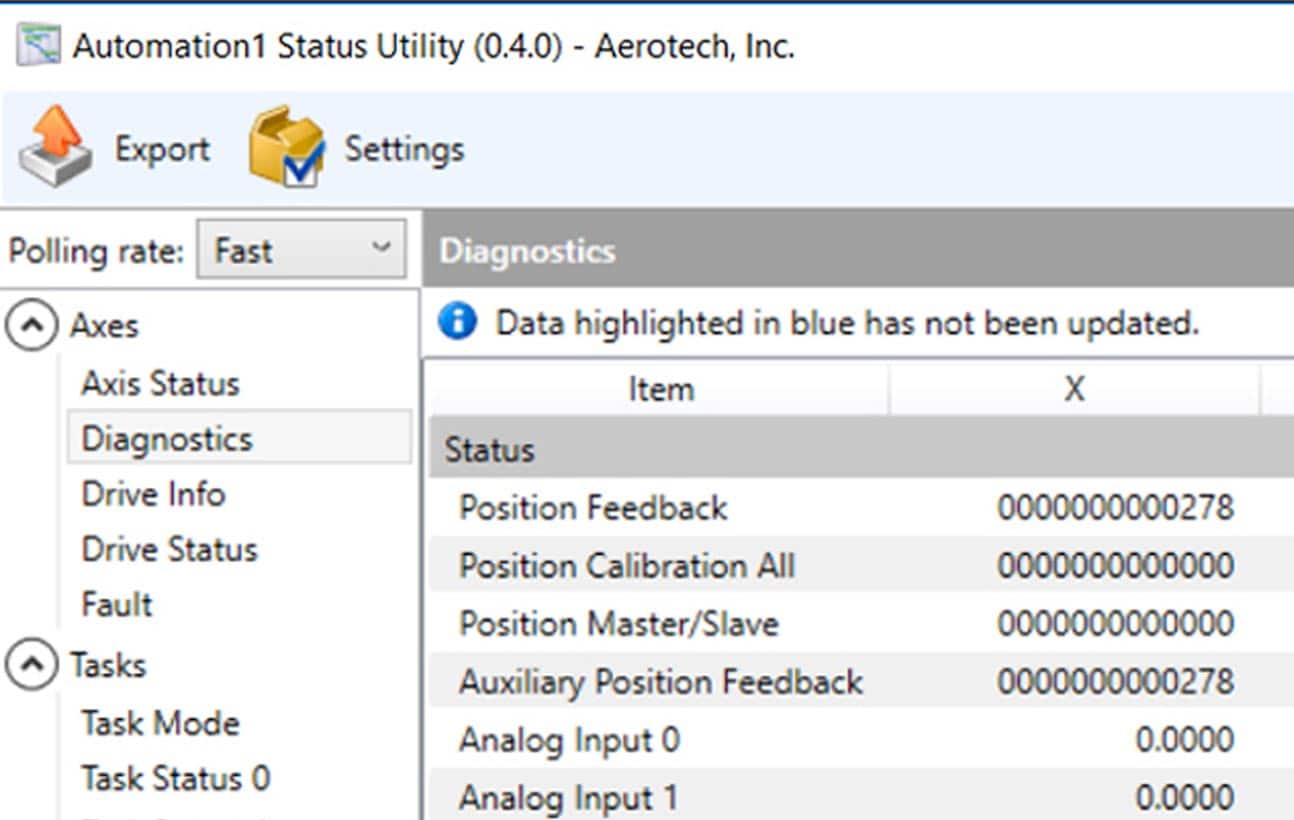
Quickly enable, home and jog axes from the axis dashboard. Built for flexibility, the axis dashboard includes a minimized view, maximized view and maximized view with jog controls. The dashboard’s cutting-edge design enables quick and easy control for real motion or system simulation.Â
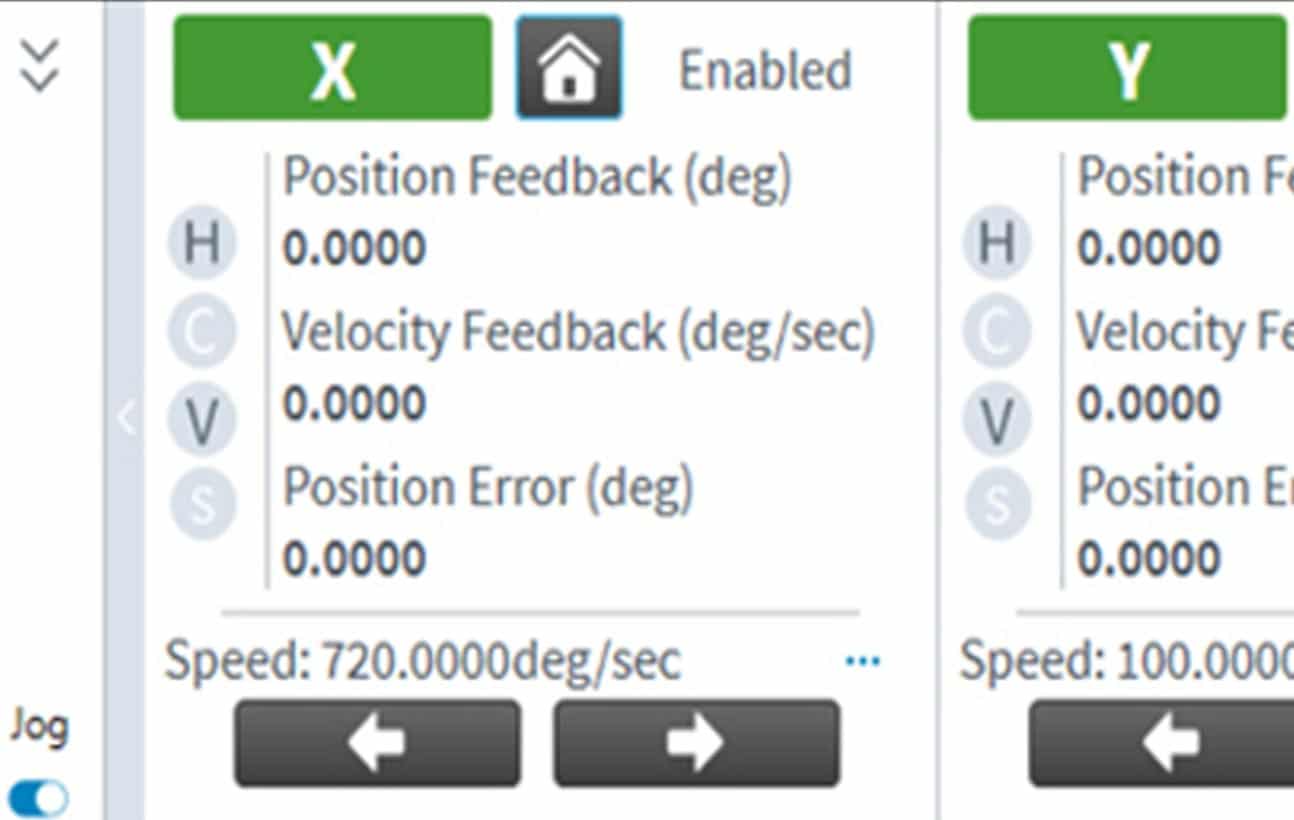
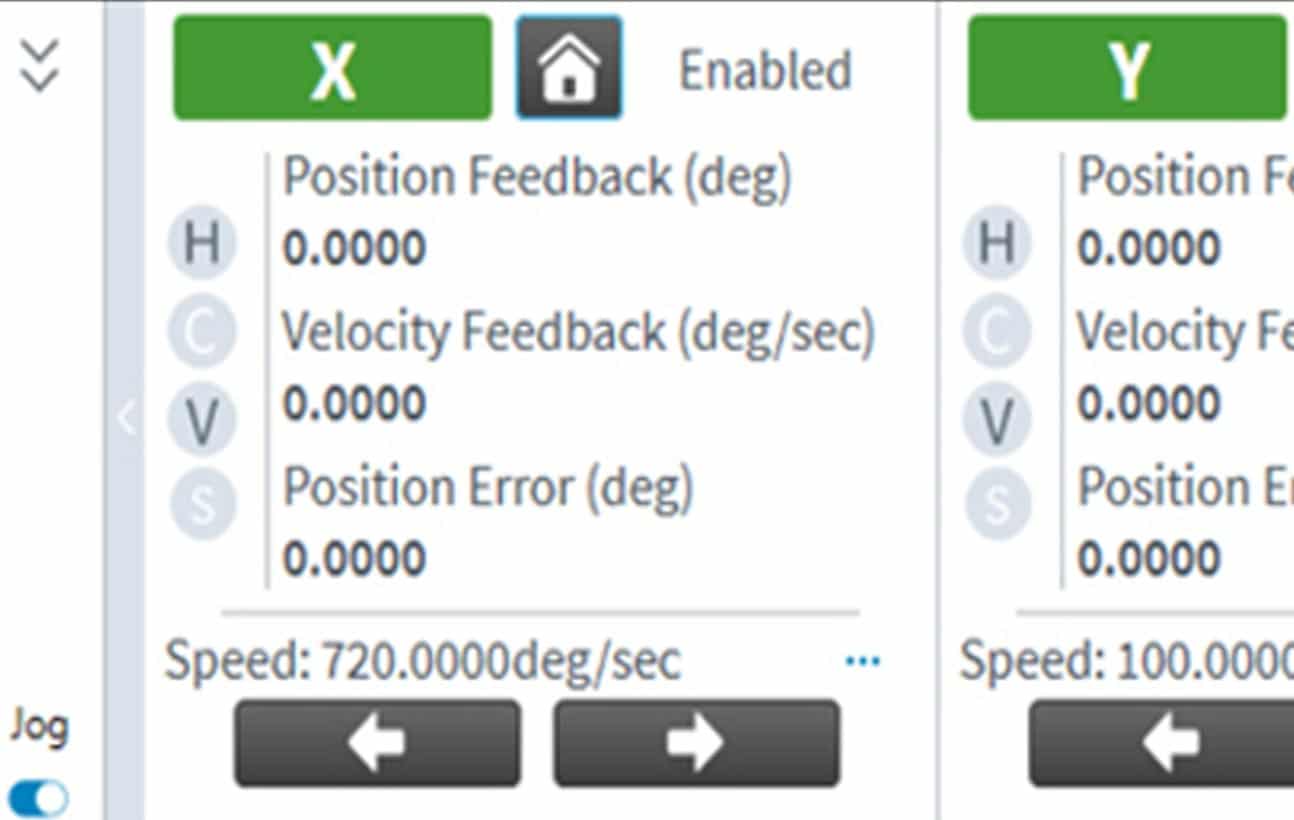
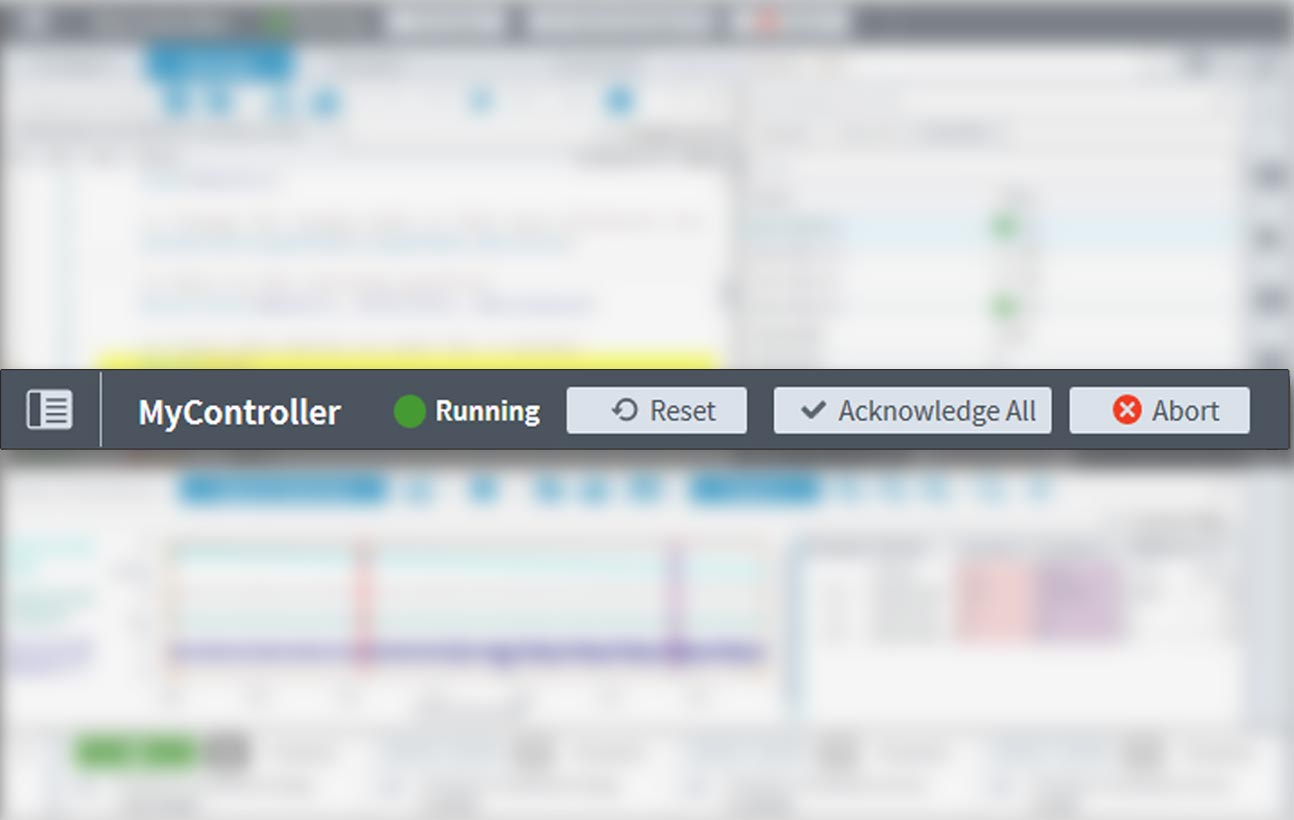
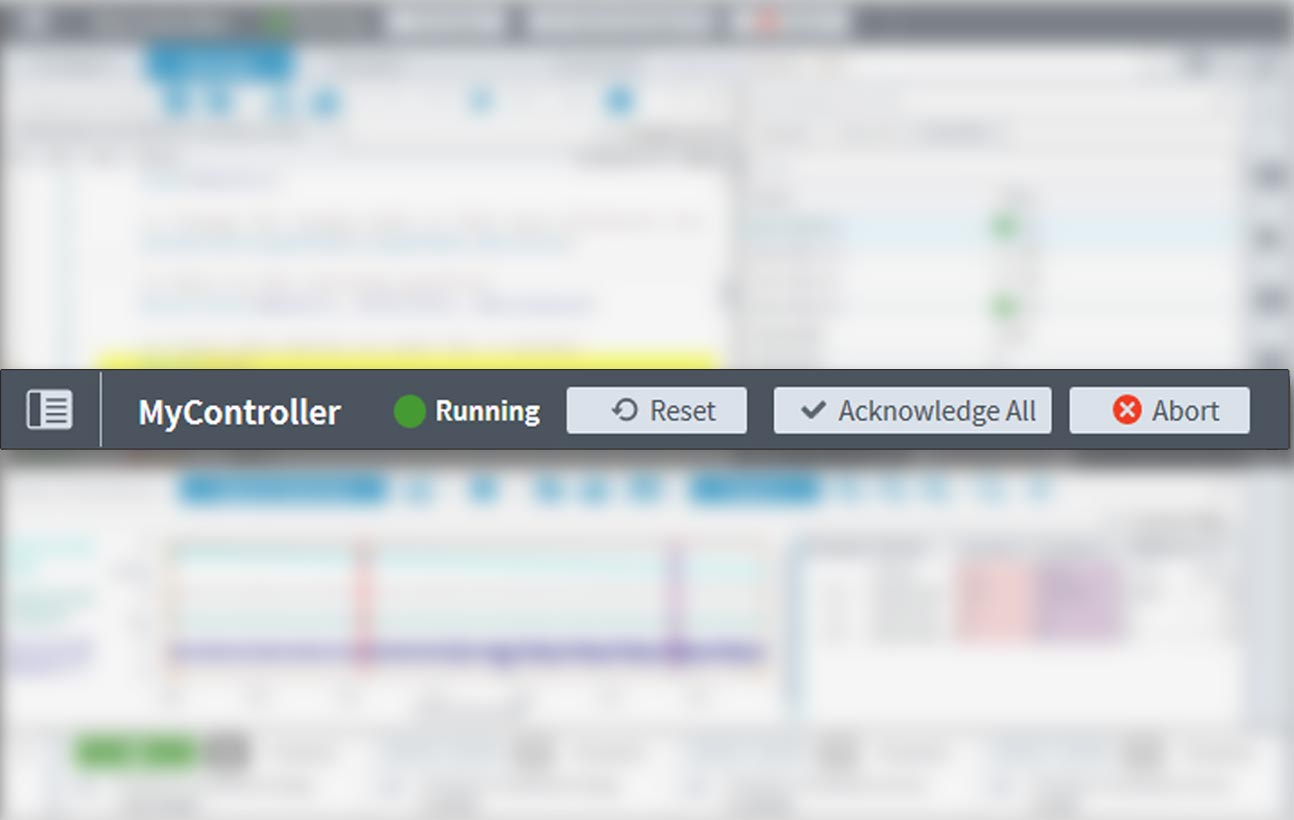
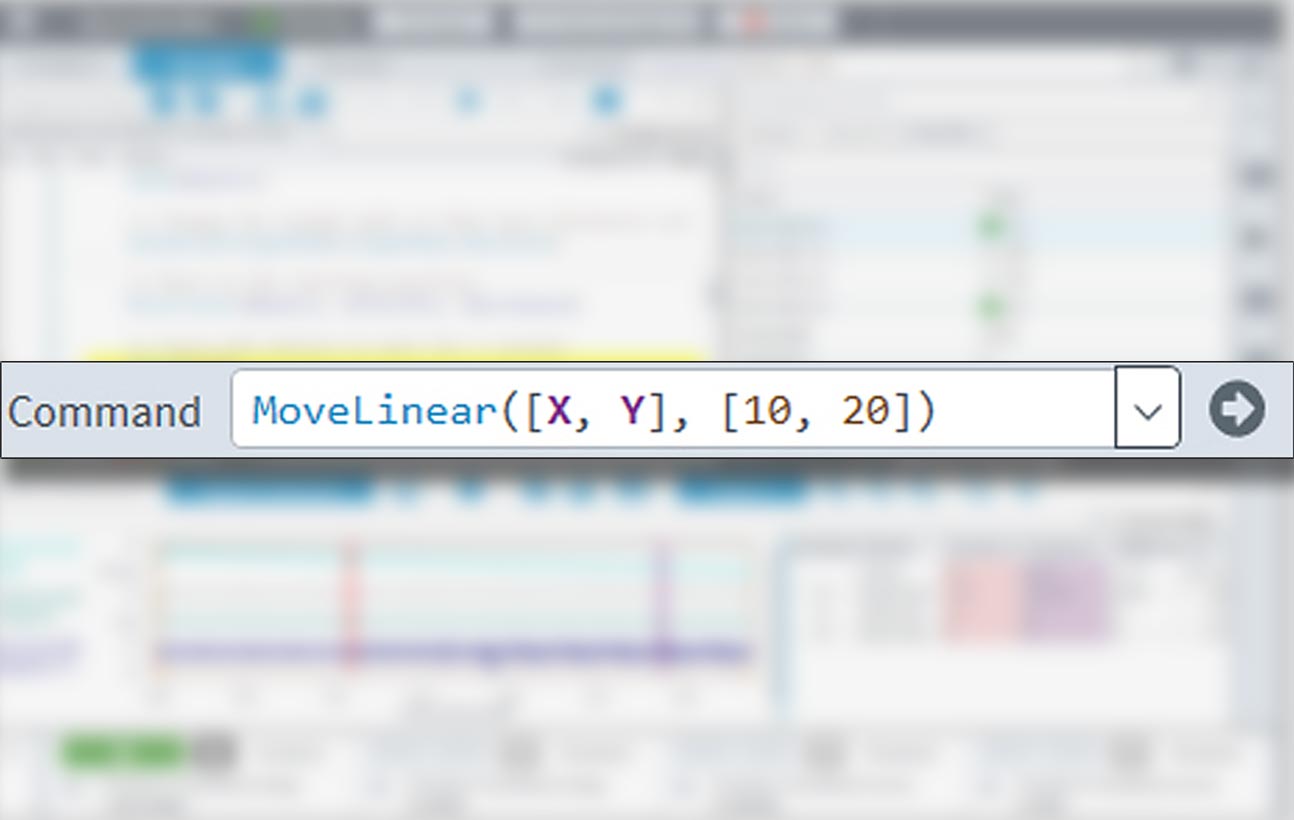
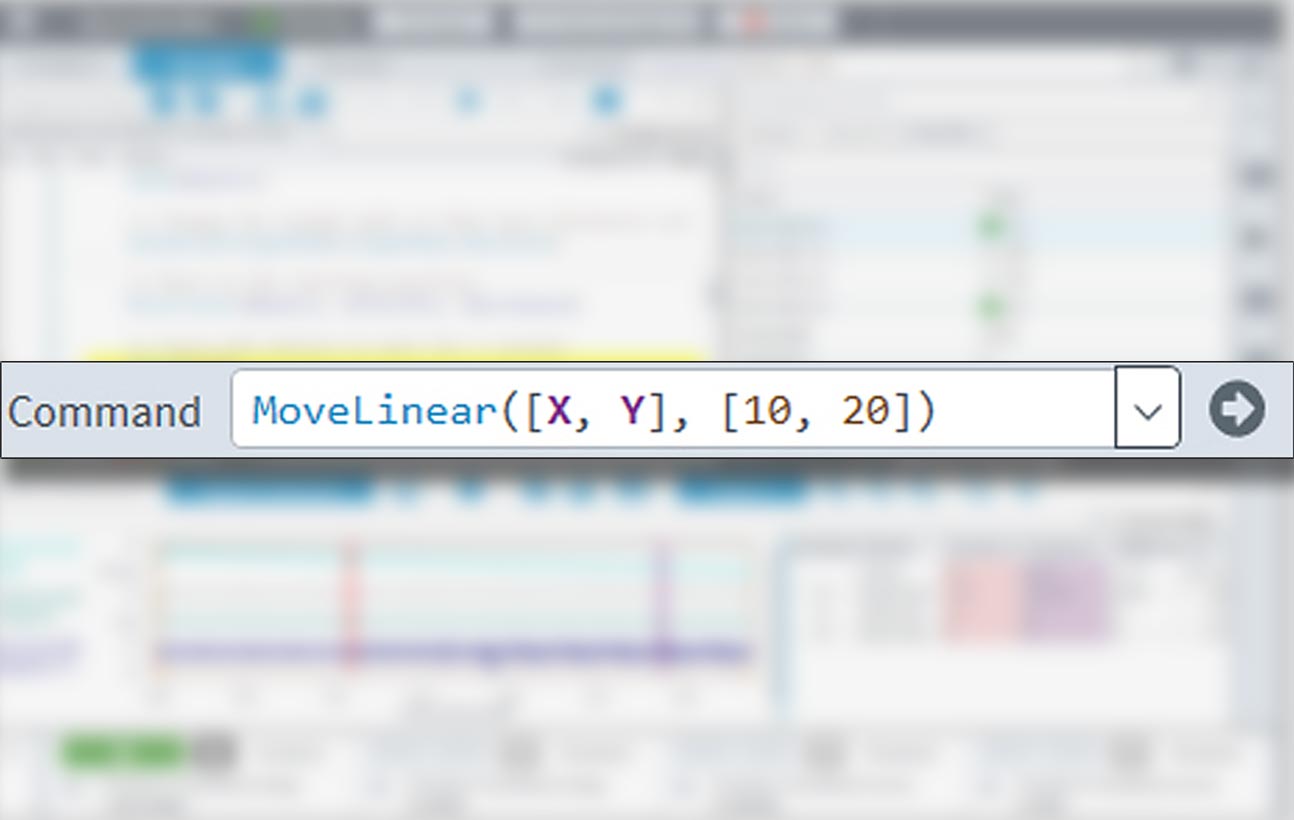
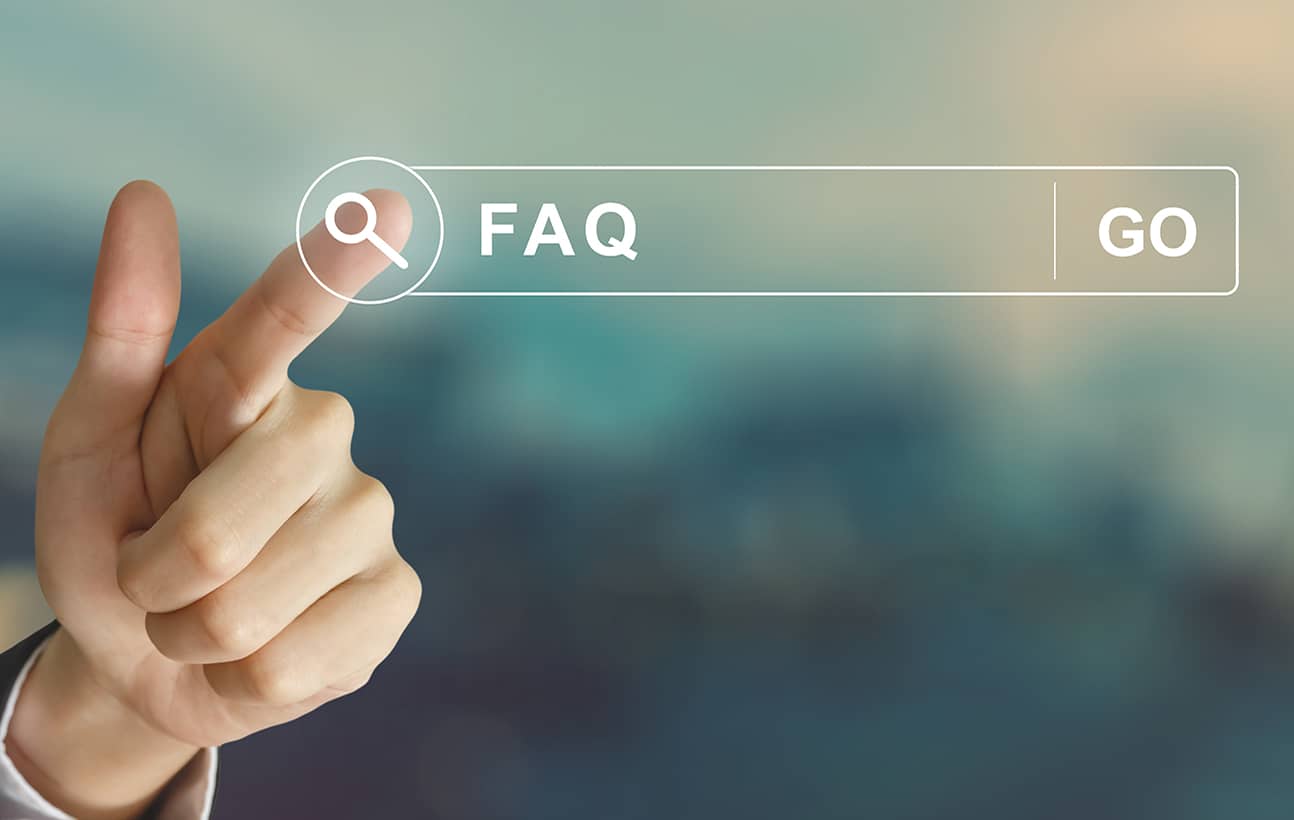
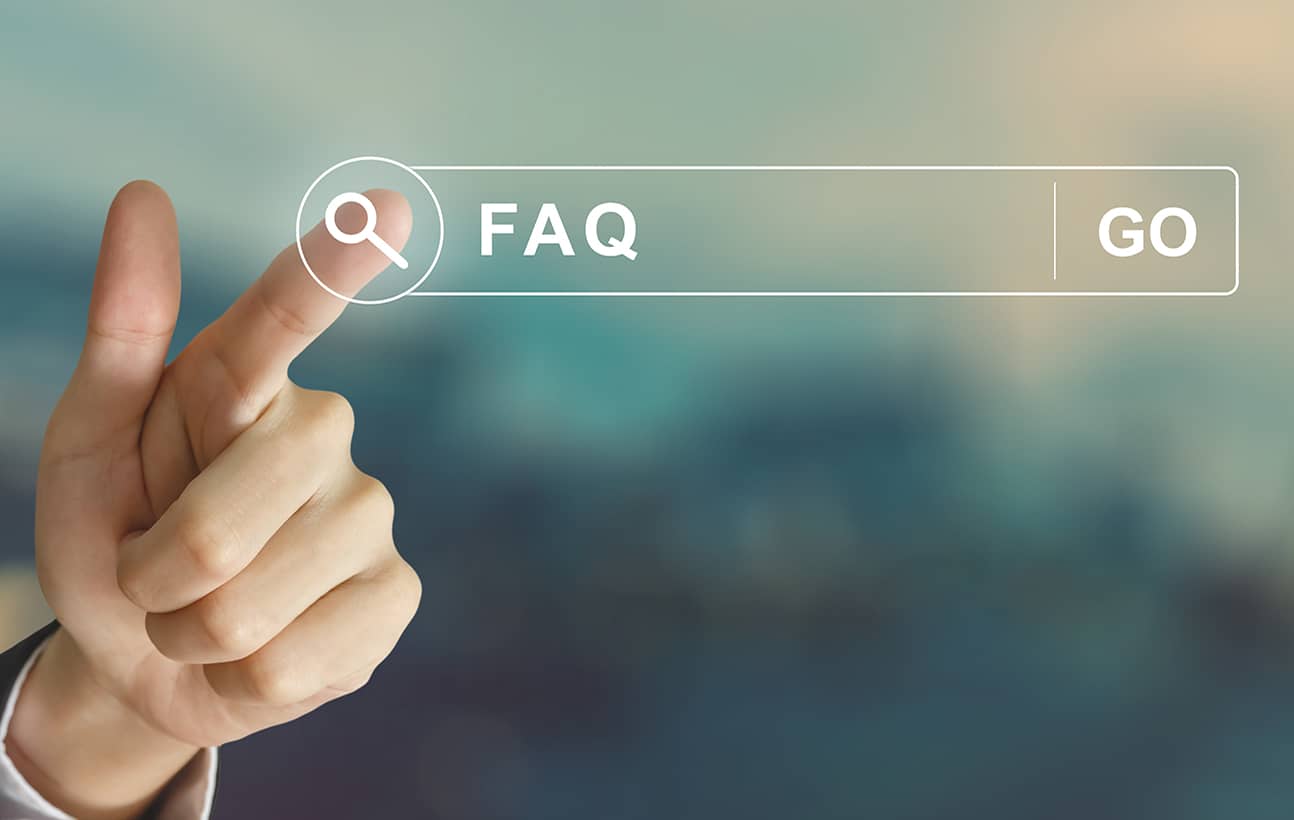