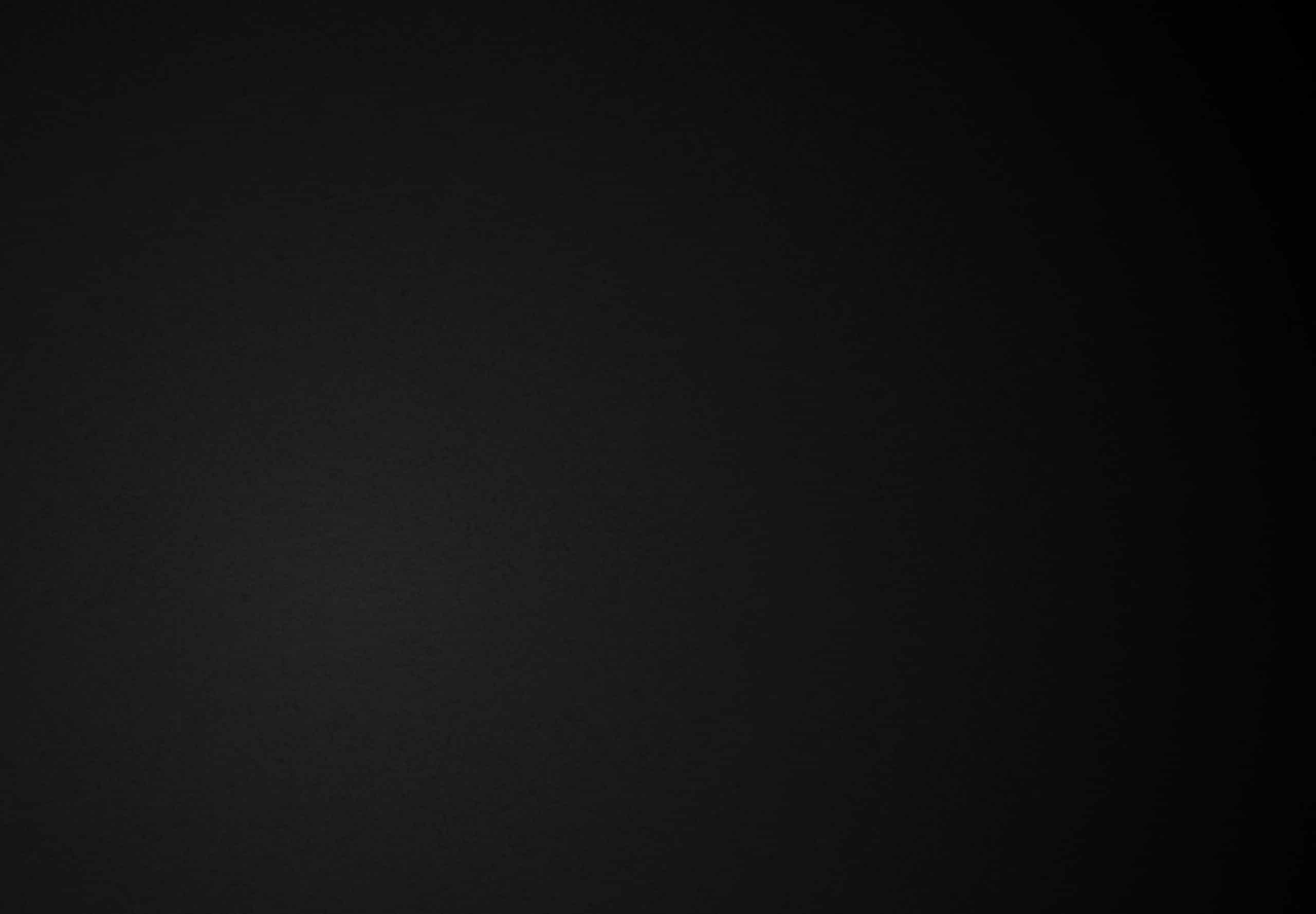
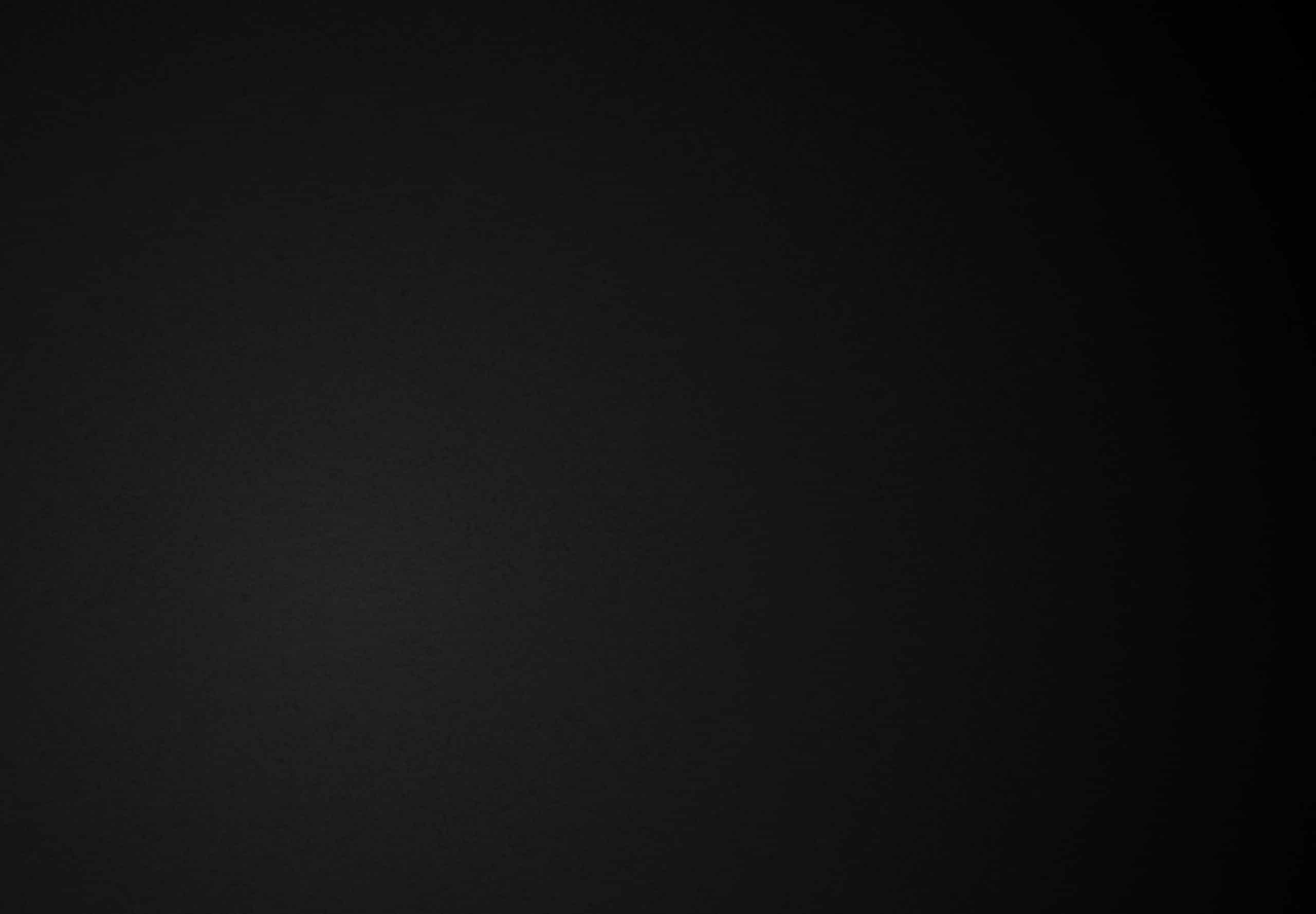
RESOURCES
The resources you need, when you need them.
Access software downloads and activations, white papers, manuals, help files, CAD files and more.
Educational Library
New Horizons in Cardiac Stent Manufacturing
Since the early 1990s, a procedure to widen cardiology patients’ blocked or narrowed arteries—percutaneous coronary intervention (PCI)—has used metal stents. These bare metal stents have proven to be particularly useful in addressing elastic compression that reduced efficacy of traditional balloon devices for maintaining desired arterial widening.
Precision Laser Material Processing: The Definitive Guide
In modern manufacturing, where demands for miniaturization, complexity and…
How to Select a Precision Automation System for High-Volume Optical Alignment
Complex optical alignment processes demand precision motion systems that balance alignment accuracy, repeatability and speed. But how do you choose the best solution for high-volume production? This webinar provides a deep dive into precision automation technologies for high-volume active alignment processes. Learn how to overcome positioning challenges and improve manufacturing efficiency with the right motion control technology.
Automation1 Version 2.10
Welcome to the Automation1 2.10 release update. This update…
Advanced Motion Control for Semiconductor Metrology
Are you facing the ever-increasing demands for accuracy, speed and reliability for your semiconductor inspection and metrology tools? This webinar provides a comprehensive overview of advanced motion control fundamentals and key technologies specifically tailored to address this industry’s unique challenges.Â
DrillOptimizer for Galvo Scanner Systems
Aerotech’s DrillOptimizer, an advanced feature of AeroScriptPlus, is designed…
The Aerotech Difference – Brain Computer Interfaces
See how leading Brain Computer Interface (BCI) device developers…
Advancing Implantable Medical Device Reliability with Enhanced Laser Joining Technology
In the realm of high-performance, Class III implantable medical devices, laser joining is the gold standard for assembly. This technology enables the production of many medical innovations, from passive devices like guidewire assemblies to sophisticated active products such as cardiac rhythm modulation (CRM) devices and brain-computer interfaces (BCIs). Manufacturers need to know – with certainty – that device components will maintain their integrity once deployed within a patient. Laser joining addresses this critical need by offering a non-contact, particulate-free joining method, high-strength bonds formed at rapid speeds, and exceptional precision and controllability.
Harnessing laser joining’s full potential hinges on precise process control. The location and amount of thermal energy the laser applies to the materials to form a high-integrity bond is instrumental in ensuring consistent, reproducible joints with minimal heat-affected zones. By pairing advanced controller features such as spatial domain laser pulse control with superior electromechanics, device manufacturers can achieve unprecedented levels of part reproducibility in their assembly processes. These control features enhance joining processes to pave the way for increasingly complex and miniaturized implantable devices, ultimately leading to better patient outcomes and expanded treatment options.
Automation1 Command Queue
Aerotech is a company that solves your toughest precision motion and automation challenges. Automation1 is a motion control platform consisting of:
– software-based controls and development tools
– PC and drive-based control hardware, AND
– hardware-based drives for servo motors and other devices.
In this video, you will discover… the benefits of Command Queue and an example configuration.
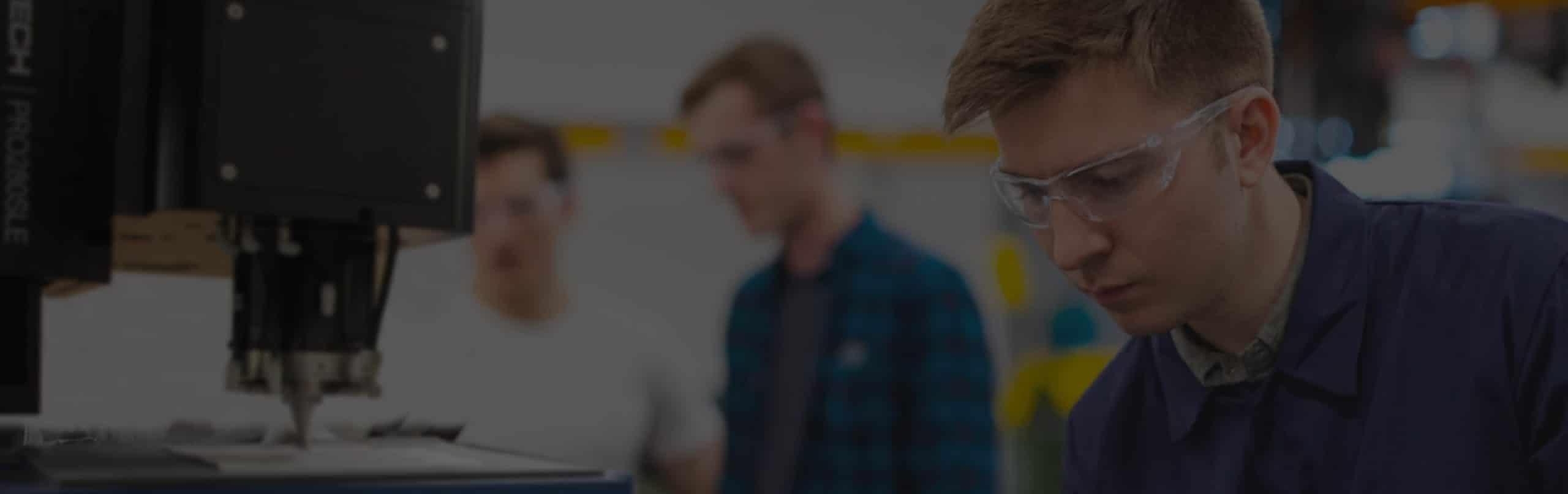
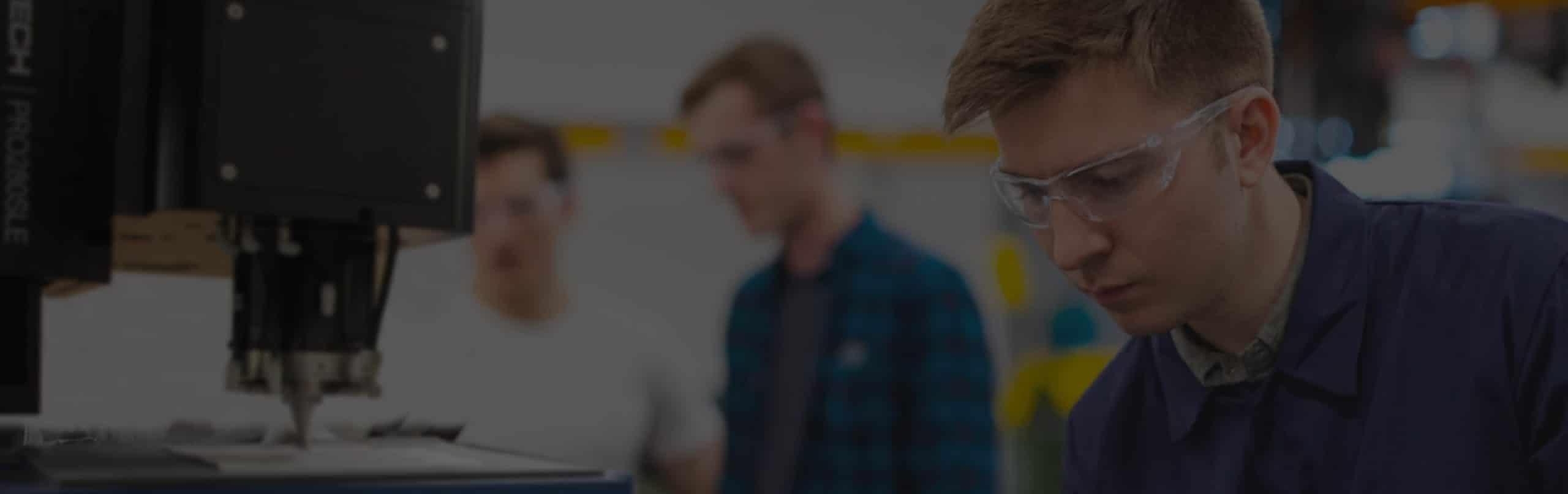