Webinar
How to Tune Servo Systems: Force Control
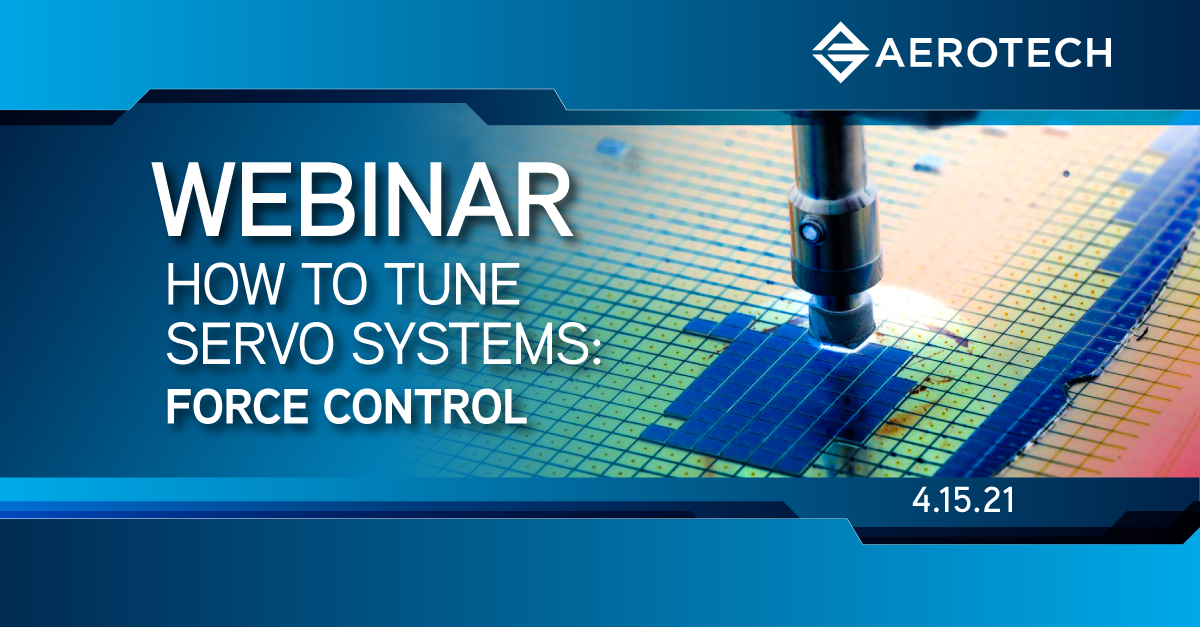
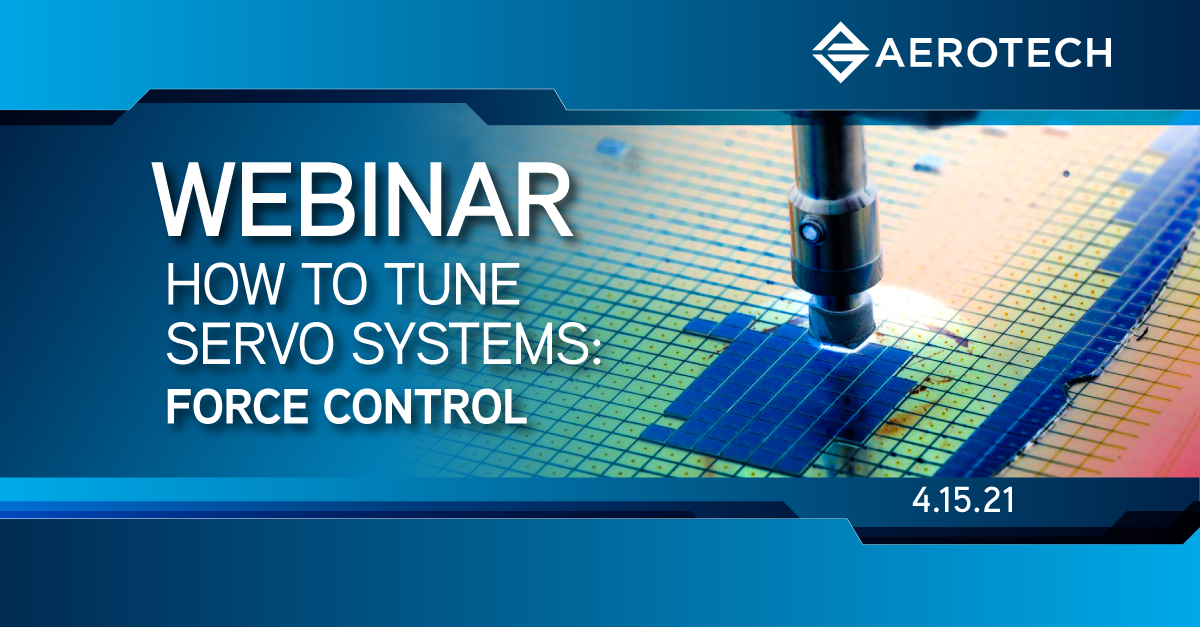
About the Webinar
Among the most troubling tasks in machine building can be tuning the servo system to meet or exceed the performance specification. Invariably, we have all sat at the machine and asked ourselves, “What three numbers should I put in this proportional-integrated-derivative (PID) controller?” However, when tuning, it is not always about the PID gains. Many other factors affect the tuning and can be changed to improve the machine performance. This webinar will discuss aspects of controller design, including control loop structures, and using frequency-based tools for gain selection, filter selection and machine characterization. This webinar series will be presented in four parts.
Learning Objectives
Presenter Joseph Profeta, who has nearly three decades of experience working on challenging automation solutions for a variety of industries, will explain the steps he takes to optimize the performance of motion systems.
Parts one and two addressed basic tuning strategies and how to tune for optimal performance. Part three illustrated how feedback resolution and servo sample time affect servo system performance, as well as how these parameters affect the PID and feedforward gains when tuning digital control systems.
Part four of this webinar series will focus on controlling the force applied to a test specimen or part during manufacturing. Various control loop configurations will be covered, along with how to tune the force loop. Both static and dynamic force trajectories will be discussed. You will learn:
- The limitations of a force loop around the position and current loops;
- How to command arbitrary force trajectories; and
- How to minimize the bump when transferring between position and force mode.
Who Should Attend
Engineers and researchers who design and build automation equipment with servo technology to achieve medium- and high-performance control of position, velocity and/or force would benefit from attending. The webinar would be helpful to those involved in a wide range of automation applications from laser processing, semiconductor inspection, die bonding, winding applications, and labelling systems.
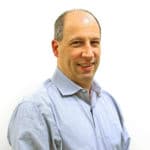
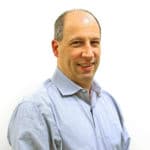
Dr. Profeta has more than 30 years of experience in technology-driven companies. He is the director of Aerotech’s controls system group with P&L responsibility for controls, drives and motors. In this role, he works with companies to design and select control system architectures that result in increased machine performance while minimizing component cost. He has earned bachelor’s, master’s, doctoral degrees, as well as an executive MBA. He has been awarded five patents and published 43 papers. Joe is also an adjunct professor in the electrical and computer engineering department at the University of Pittsburgh where he teaches software engineering and mechatronics. You can contact him at jprofeta@aerotech.com or +1 412-967-6839.