3D Metrology Systems, Aerospace & Defense, Application Note, Data Storage, Electronics, Motion Control Platforms, Optics & Photonics, Piezoelectric Nanopositioners, Precision Manufacturing, Science & Research Institutions, Semiconductor, Stages & Actuators, Test & Inspection
Application Note
Automation1 Servo Drives Improve In-Position Stability
When it comes to characterizing precision mechatronic systems, a meaningful system performance test is the measurement of in-position stability or in-position jitter. In this test, the axis is commanded to hold a target position and the small motion of the mechanical positioning axis is measured. Many applications require nanometer-level positioning and little-to-no motion when commanded to hold a position. The in-position jitter test quantifies the level of noise that can be expected in these applications.
Aerotech’s Automation1 motion control platform offers significant in-position jitter improvements over our previous generation of control products. Figure 1 shows an image of Aerotech’s Automation1 software and some hardware products.
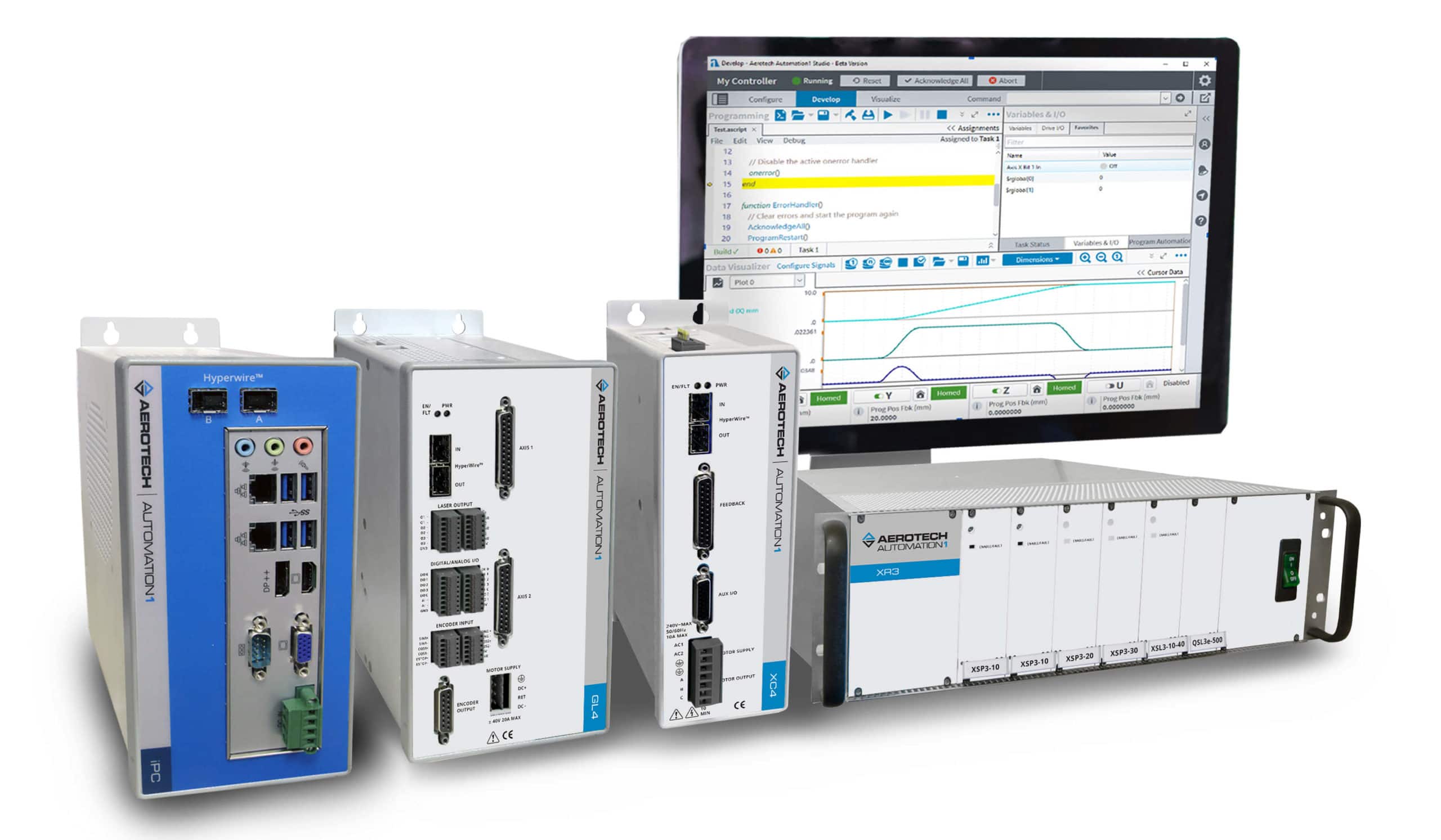
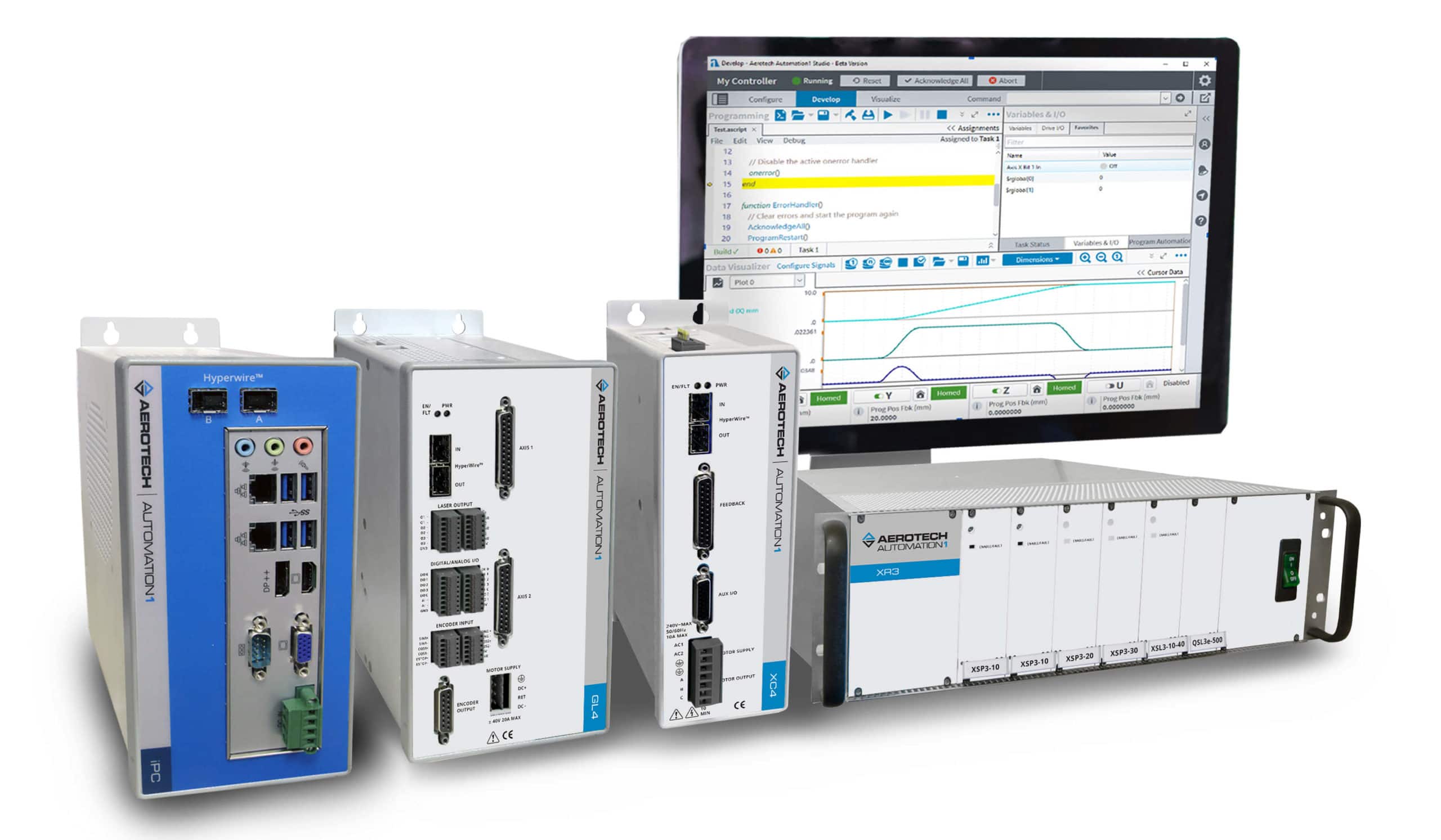
Air Bearing Stage Drive Performance Tests
An air bearing stage provides a great positioning system to measure in-position jitter induced by control and drive electronics due to the absence of mechanical friction in the positioning stage. Tests were conducted using an Aerotech ABL1500 air-bearing direct-drive linear stage. The stage, driven by an Aerotech BLMC series brushless linear motor, is mounted to a granite base on a passive air isolation system, supported by a steel weldment. The in-position stability was measured using the integral encoder feedback signal, a 1 Vpp amplified sine-wave encoder with a 4 μm encoder scale pitch. The stage was commanded to hold position and the in-position noise, as read by the encoder, was recorded and analyzed.
Tests were performed on the Automation1 XR3 multi-axis drive rack with two different slice amplifiers. These tests were compared to the in-position jitter performance of a Npaq drive rack. In addition, the Automation1 XL5e, Automation1-XC2e, and Automation1-XL2e servo motor drives were compared to the performance of the A3200 Ndrive HLe drive.
Table 1. In-position jitter noise tests on an ABL1500 as measured by the stage encoder.
ABL1500 Air Bearing Tests | |||||
---|---|---|---|---|---|
Automation1 | A3200 | ||||
Amplifier | In-position jitter | Amplifier | In-position jitter | ||
XR3: XSP (PWM) | 1.5 nm, rms | Npaq: DP32010e (PWM) | 4.8 nm, rms | ||
XR3: XSL3 (Linear) | 0.6 nm, rms | Npaq: DL4010 (Linear) | 2.8 nm, rms | ||
XL5e (Linear) | 0.8 nm, rms | Ndrive HLe (Linear) | 3.3 nm, rms | ||
XL2e (Linear) | 0.9 nm, rms | ||||
XC2e (PWM) | 1.2 nm, rms |
Gantry Bridge-Axis Drive Performance Tests
Tests were conducted using the bridge axis of an Aerotech AGS10000 gantry. This axis was driven by an Aerotech BLM-264-A motor and carried an ATS150 Z-axis. The gantry was mounted on a passive isolation material supported by a steel weldment. The in-position stability was measured using the integral encoder feedback signal, a 1 Vpp amplified sine-wave encoder with a 20 μm encoder scale pitch. The stage was commanded to hold position and the in-position noise, as read by the encoder, was recorded and analyzed.
The Automation1 XR3 PWM amplifier was tested against the A3200 Npaq PWM amplifier. The Automation1 XC4e and Automation1 XC4 were tested compared to the Ndrive HPe and Ndrive CP drives, respectively. The results are shown in Table 2.
Table 2. In-position jitter noise tests on an AGS10000 bridge-axis as measured by the stage encoder.
Automation1 | A3200 | ||||
---|---|---|---|---|---|
Automation1 | A3200 | ||||
Amplifier | In-position jitter | Amplifier | In-position jitter | ||
XR3: XSP (PWM) | 1.5 nm, rms | Npaq: DP321010e (PWM) | 4.5 nm, rms | ||
XC4e (PWM) | 0.9 nm, rms | Ndrive HPe (PWM) | 1.3 nm, rms | ||
XC4 (PWM) | 4.9 nm, rms | Ndrive CP (PWM) | 7.9 nm, rms |
Cross-Roller Bearing Stage Drive Performance Tests
Tests were conducted using a cross-roller bearing linear stage driven by an Aerotech linear motor. The stage was mounted to a granite table with passive air isolation supported by a steel weldment. The in-position stability was measured using the integral encoder feedback signal, a 1 Vpp amplified sine-wave encoder with a 4 μm encoder scale pitch. The stage was commanded to hold position and the in-position noise, as read by the encoder, was recorded and analyzed.
The Automation1 XR3 linear and PWM amplifiers, as well as the Automation1 XL2e, Automation1 XC2e and Automation1 XC2 were tested on a common platform. They are each being compared to the A3200’s Ndrive MP, which was tested on a similar platform at an earlier date. The results are shown in Table 3.
Table 3. In-position jitter noise tests on a cross-roller bearing linear stage as measured by the stage encoder.
Cross Roller Bearing Stage Test | |||||
---|---|---|---|---|---|
Automation1 | A3200 | ||||
Amplifier | In-position jitter | Amplifier | In-position jitter | ||
XR3: XSL (Linear) | 0.11 nm, rms | N/A | - | ||
XR3: XSP (PWM) | 0.20 nm, rms | N/A | - | ||
XL2e (Linear) | 0.12 nm, rms | N/A | - | ||
XC2e (PWM) | 0.18 nm, rms | N/A | - | ||
XC2 (PWM) | 0.20 nm, rms | Ndrive MP (PWM) | 0.6 nm, rms |
1.) Two significant digits are displayed in order to highlight the performance differences.